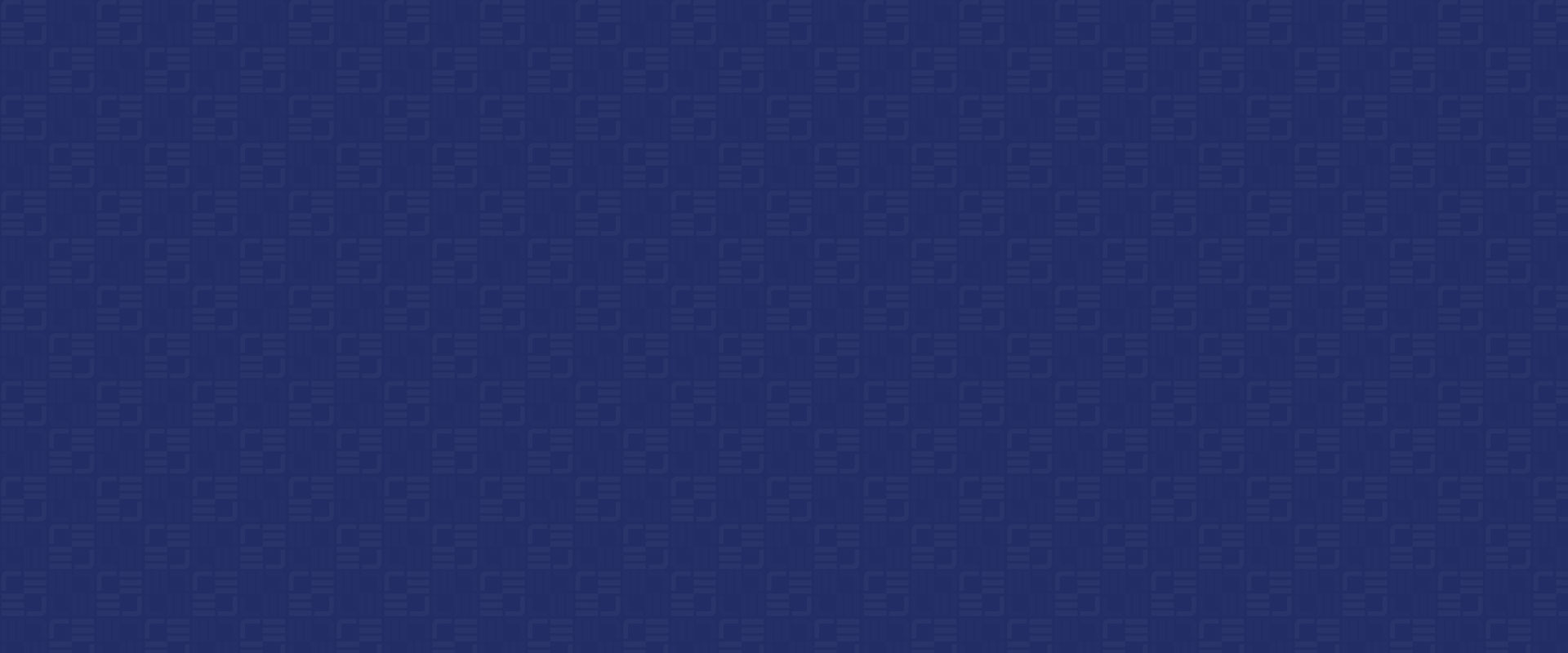
Categoría: Torres de refrigeración.
Uno de los primeros factores a tener en cuenta es cómo se montan los paquetes es si son encolados o ensamblados mecánicamente (MA). En pocas palabras, los requisitos de resistencia para la mayoría de las aplicaciones estándar en una torre de refrigeración pueden satisfacerse tanto con paquetes MA como pegados. Consulte nuestro artículo donde podrá leer una comparación detallada de los paquetes pegados y ensamblados con MA.
El grosor de la lámina viene determinado por la aplicación. Por ejemplo, una torre de refrigeración montada sobre el terreno a contracorriente que preste servicio a una central eléctrica suele tener un requisito más exigente en cuanto a la fuerza admisible del paquete porque los miembros del equipo de servicio caminarán sobre la parte superior de los paquetes de relleno para realizar el mantenimiento de las boquillas. También esperan una vida útil más larga en entornos duros y donde no quieren que se dañen los paquetes. Para este tipo de torres, vemos como norma espesores de chapa postformada de 15 y 20 milímetros. Compare esto con una torre de refrigeración de contraflujo montada en fábrica que está dando servicio a una escuela local. En este caso, el equipo de mantenimiento no caminará ni pondrá cargas pesadas en los paquetes de relleno. La aplicación de refrigeración de confort es menos crítica, lo que permite ahorrar costes utilizando láminas de 8 y 10 milímetros de espesor después del conformado como norma. Cuanto más gruesa sea la lámina, mayor será la resistencia al aplastamiento esperada, ya que hay más material polimérico para absorber una fuerza aplicada.
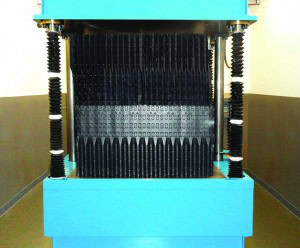
Prueba de compresión de medios de relleno
Otro aspecto que debemos tener en cuenta es el espaciado de las láminas dentro del paquete. El mejor ejemplo y el más común es comparar los rellenos CF1200 con los CF1900. El CF1200 tiene una medida de láminas de 12 mm, mientras que el CF1900 tiene una medida de láminas de 19 mm. Dado que el CF1200 tiene más láminas para el mismo tamaño de envase, utilizando el mismo grosor de lámina para ambos, el CF1200 será capaz de distribuir una carga aplicada sobre más puntos de contacto y debería proporcionar un envase más "fuerte".
Por último, pero no por ello menos importante, debemos tener en cuenta la geometría acanalada de los envases. Lo que queremos decir aquí es si el diseño del paquete es un corrugado cruzado, un estriado desplazado, un estriado vertical u otro diseño. Debido a la geometría de los canales dentro del diseño del paquete, obtenemos paquetes con resistencias inherentemente diferentes, de forma muy parecida a la diferencia entre una viga de madera de ingeniería LVL y la viga de la misma dimensión hecha de un tronco sencillo. Un paquete corrugado cruzado, como un CF1200 o CF1900, es inherentemente más resistente al aplastamiento debido a su geometría de canales cruzados frente al mismo paquete diseñado en una disposición de canales verticales. Tener un diseño de hoja de relleno que cruza las flautas en ángulos opuestos hace que haya más puntos de conexión y un paquete más fuerte que uno en el que las flautas están todas alineadas en la misma dirección e instaladas en paralelo.
Por supuesto, dicho todo esto, el aspecto importante del diseño que no podemos pasar por alto es el diseño y el espaciado de los soportes de relleno. Esto es muy importante porque los apoyos del relleno pueden variar en anchura y los apoyos pueden variar en distancia entre apoyos. Ambos factores dictan la superficie de apoyo que tiene el relleno para distribuir la carga y pueden ser los criterios de diseño que rijan la resistencia mínima al aplastamiento del relleno.
Ahora que hemos examinado todas las variables que intervienen en la resistencia del relleno de las torres de refrigeración, sólo hay una cosa muy sencilla que un ingeniero o propietario debe saber y pedir. Una vez que el diseñador, ingeniero o propietario de una torre decide qué relleno necesita para la aplicación en función del rendimiento térmico, el potencial de riesgo de incendio y la resistencia al ensuciamiento, lo único que tiene que hacer es pedir al fabricante que le facilite los datos de resistencia al aplastamiento de ese producto para demostrar que los paquetes cumplen su requisito. Tanto si se trata de un producto encolado como con ensamblaje MA, el método de montaje del envase no debería ser un factor limitante si las propiedades mecánicas de los envases de relleno cumplen o superan las exigidas. Sencillamente, pida al fabricante del relleno una prueba de su rendimiento y cualquier fabricante reputado le facilitará gustosamente los resultados de sus pruebas.
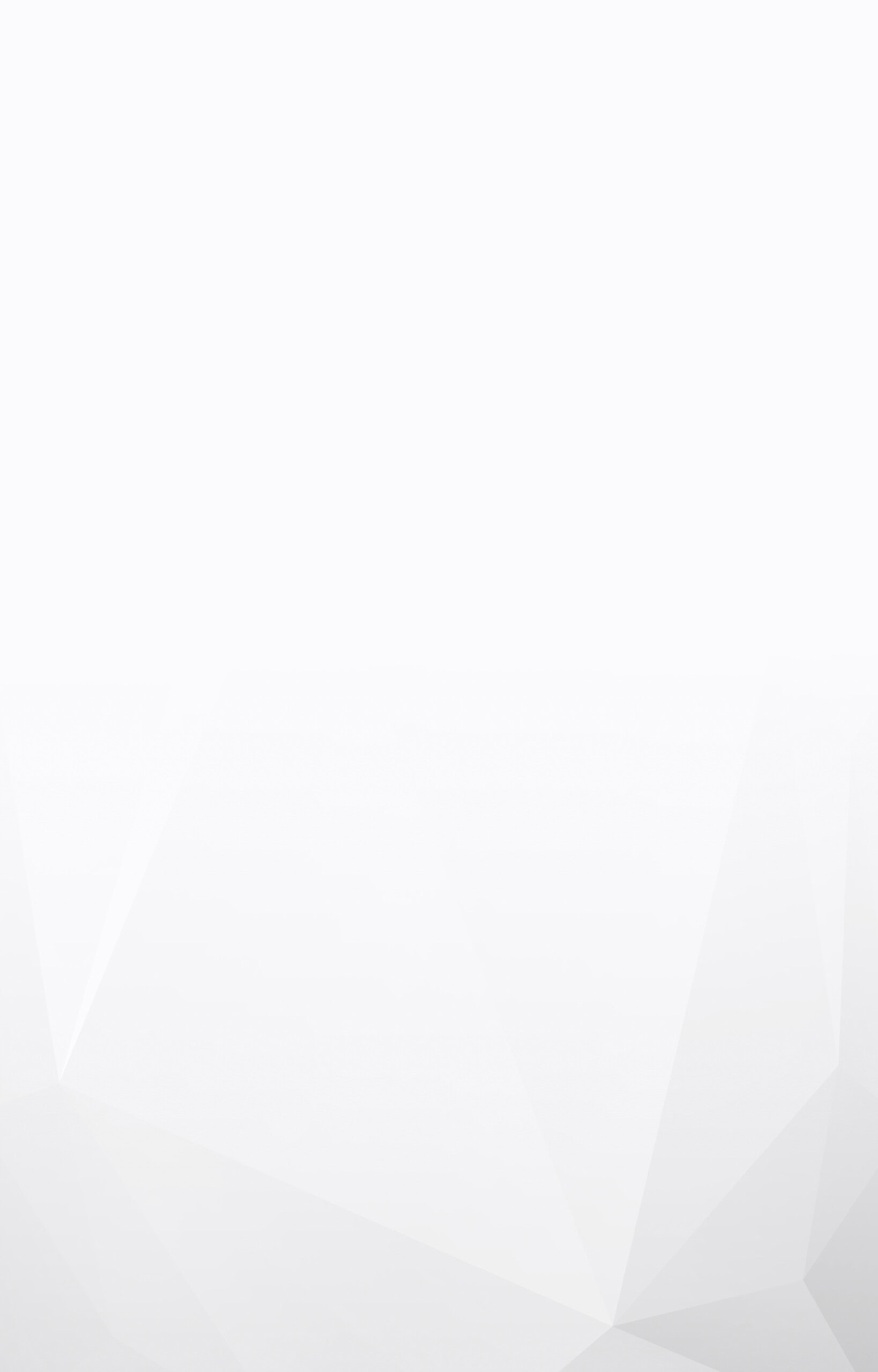