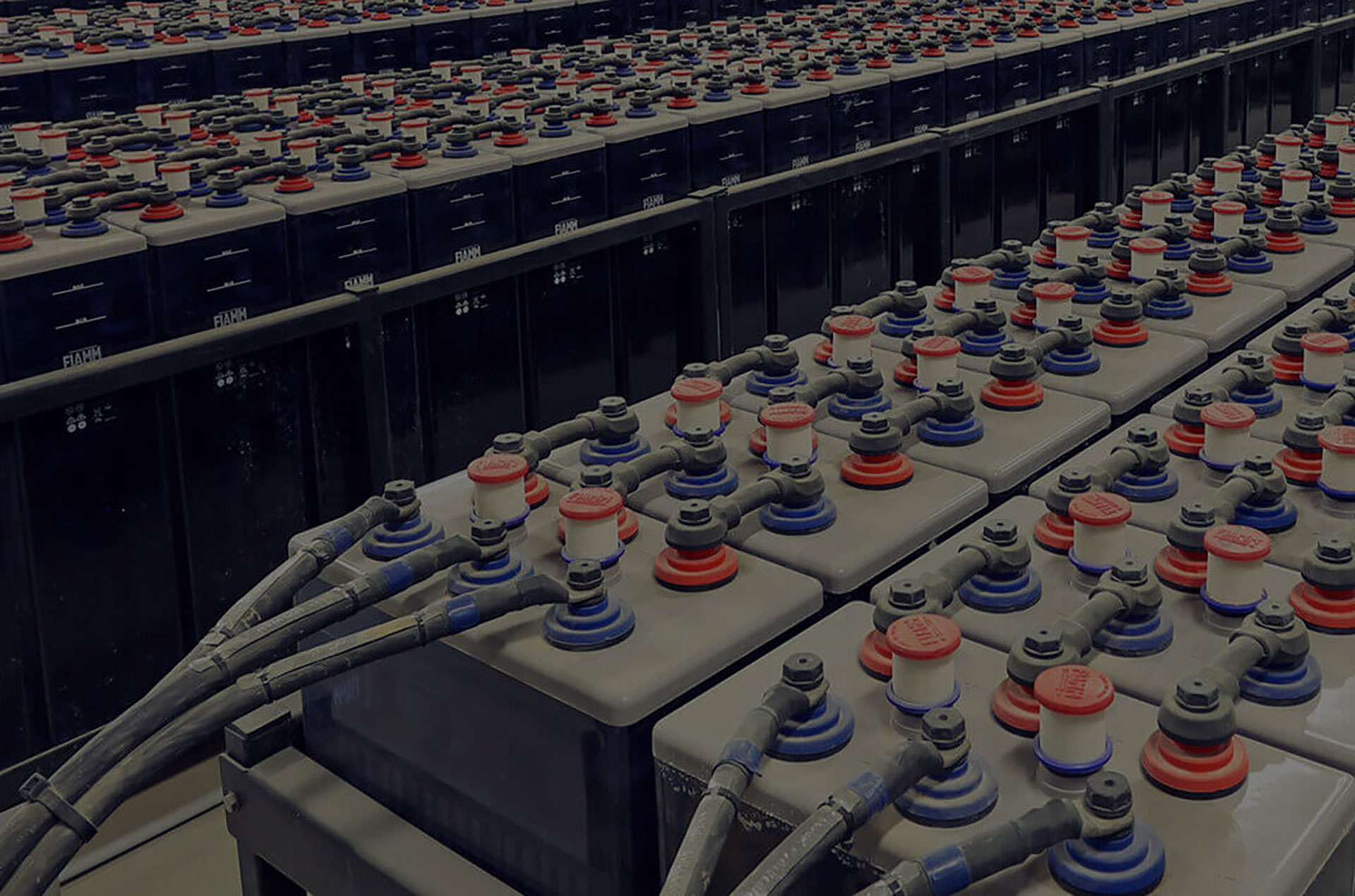
Koroseal Perforated Plate Wrap
Brentwood is a leading supplier of Koroseal, also known as perforated plate wrap or battery perf, a material used to prolong battery life by preventing corrosion of the internal lead plates. We have been manufacturing this specially formulated PVC material for nearly 40 years, since the design and installation of our first custom press machine in the 1970s.
Today, we operate a vertically integrated, closed-loop system. High-precision material blending and in-house tooling give us full control to produce top-quality Koroseal while providing design flexibility to meet your specifications.
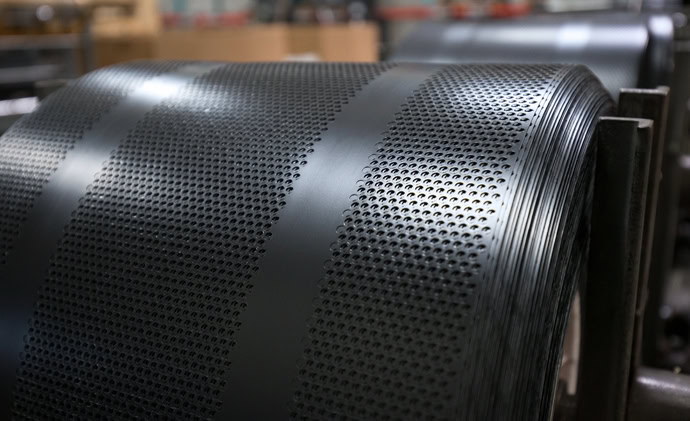
Product Details
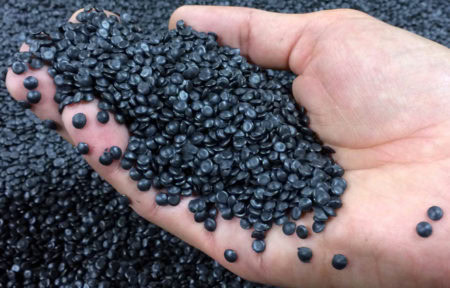
Material Formulation
Brentwood identified the correct polymer formulation for Koroseal after much trial and error in the 1970s. The specially blended PVC material is still used to make Koroseal today.
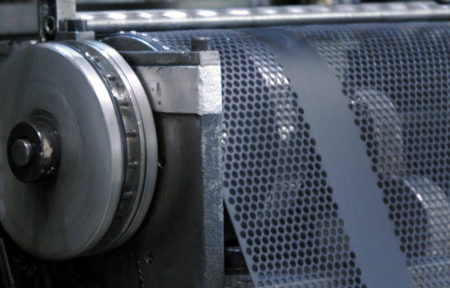
Customizable Patterns & Thicknesses
Our diverse manufacturing capabilities give us the flexibility to create custom perforations and vary border thickness to match your specific plate sizes.
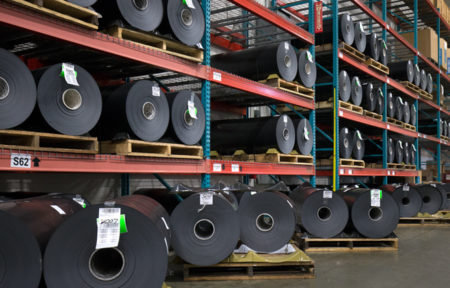
Vertically Integrated Manufacturing
Koroseal production is completely controlled by Brentwood. We create our own roll stock, perforate the plate wrap, and then take the residual punchings and recirculate them with virgin material.
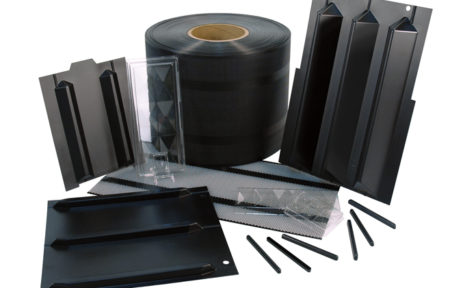
Single-Source Supplier
In addition to Koroseal, Brentwood supplies spacers, material handling trays, and in-process components to meet any of your battery manufacturing needs.
Complementary Components
Boots
Battery boots secure the Koroseal and serve as a collection point for corroded material, reducing the potential for short-circuiting. They are available in both standard and custom sizes, in addition to custom colors. Many of our boots are formed and punched in-line so we can manufacture them at higher quantities and reduce customer costs.
Spacers
Brentwood’s battery spacers provide stability and function as wedges between battery cells, extending battery life by preventing plate movement. Without this support, vibrating plates can loosen and come into contact with adjacent components and other plates, creating short-circuits that can result in major mechanical failure. Spacers can be produced in any size, based on customer requirements and specifications.
Custom In-Process Components
We make parts to fit your needs, whether that means a component that is enclosed within the battery or one that is utilized in the battery plant to aid the manufacturing process. Some examples of in-process components designed and supplied by Brentwood include vent covers, separator protectors, and charging room spacers.
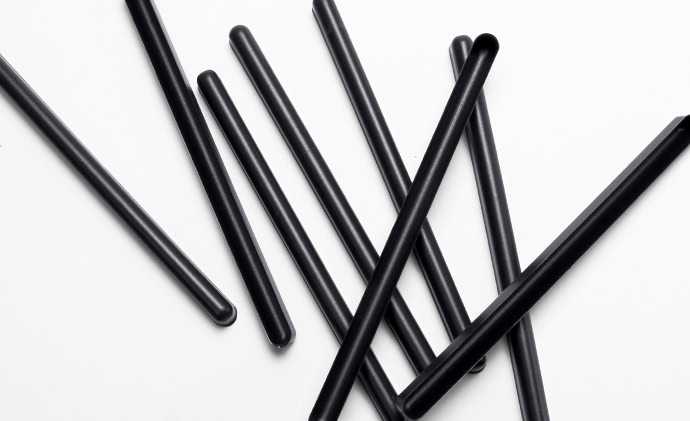
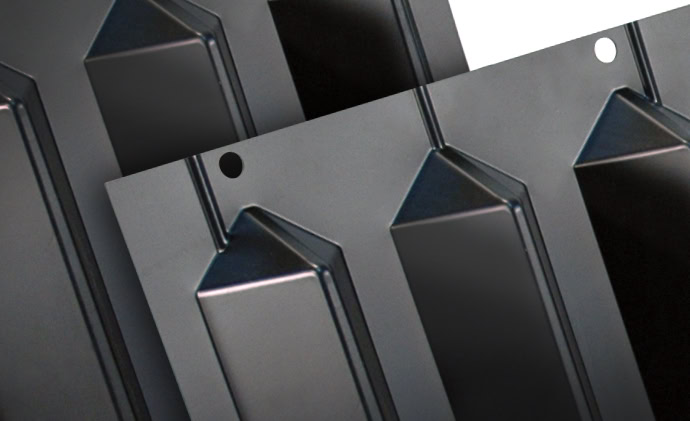
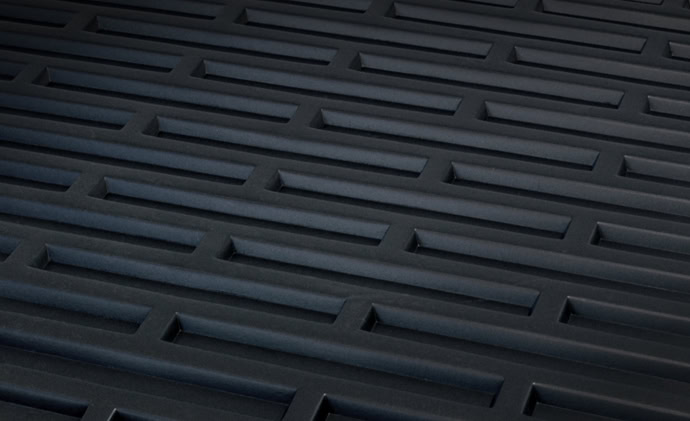
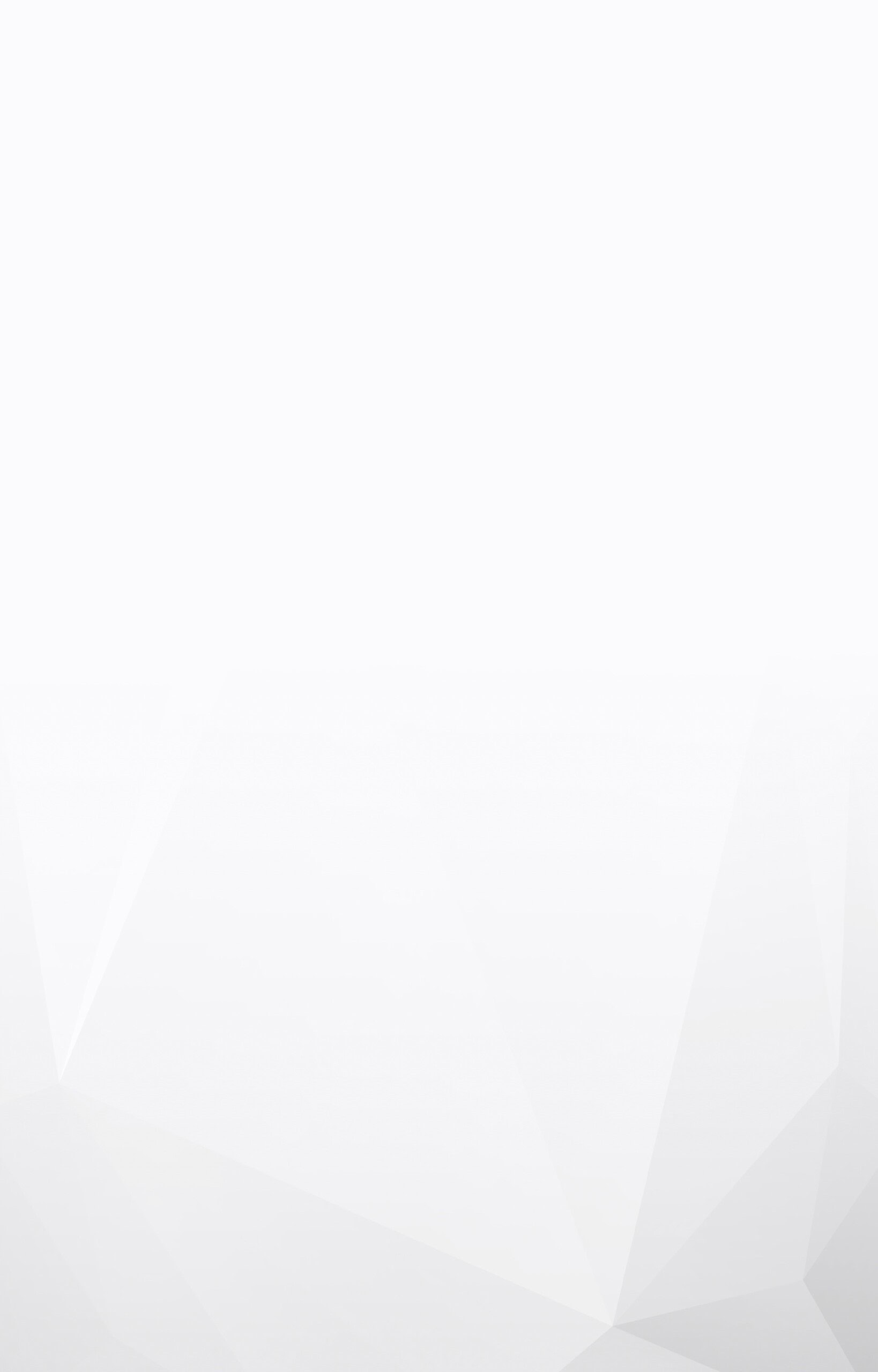