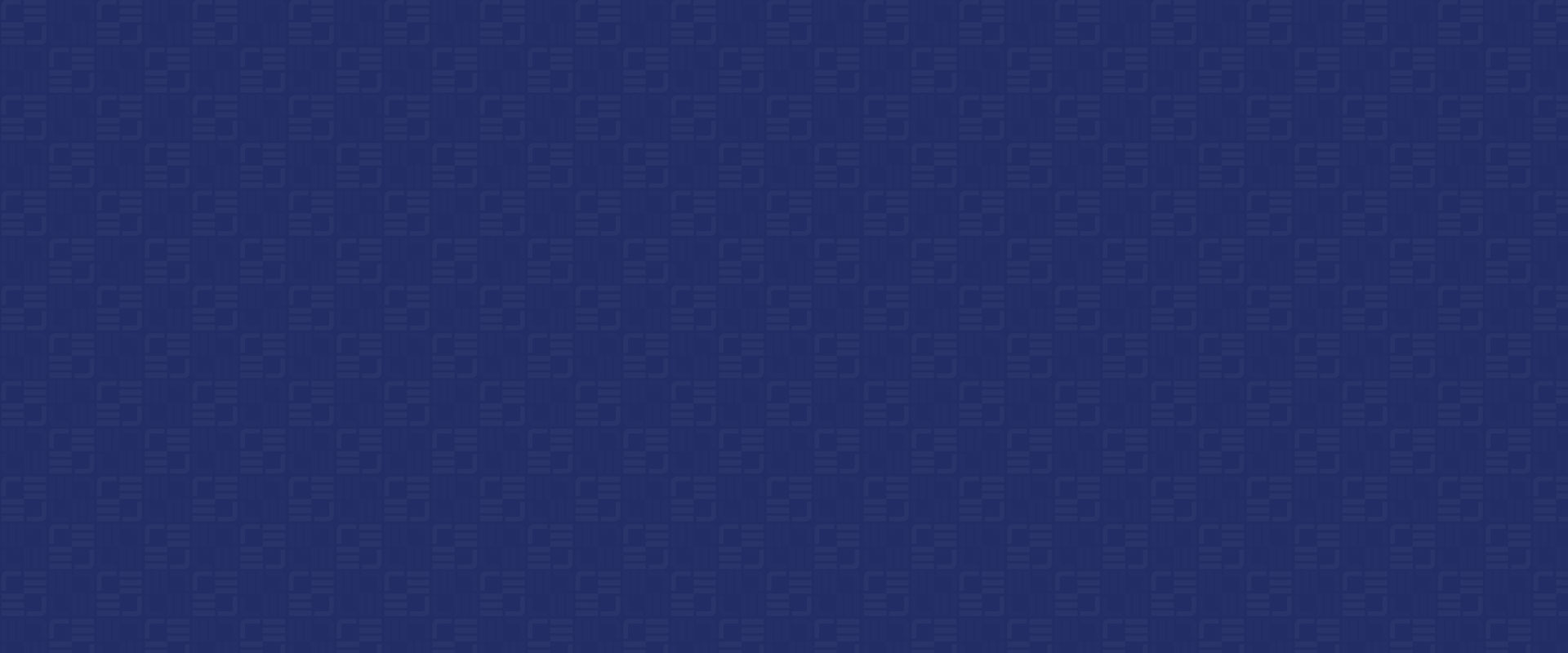
Categories: Cooling Tower.
That’s a good question that requires us to dig deeper for a full evaluation. In order to fully address the question, we need to break it down a bit. It’s good to note that Brentwood makes glued fill packs as well as Mechanically Assembled (MA) packs, so our production and engineering teams are well versed in both product types and credentialed to speak about both. Firstly, we need to understand and define what we are looking for when we say “fill pack strength.” Here we are speaking about the pack’s ability to resist crushing under a load applied in the direction of normal operating conditions because most people in the industry expect the fill packs to be strong enough to stay together under normal handling conditions for shipment and installation. To understand a fill’s crush strength we not only need to look at how the sheets are attached (glued or MA), but also the sheet thickness, sheet spacing and flute geometry.
Let’s look at glued packs. For Brentwood, the correct wording is “solvent bonding” because we utilize a solvent-based formulation to chemically weld the PVC sheet to the adjoining PVC sheet with an evaporating solvent. The term “gluing” is a carryover of years past where a substance is added to the sheets to bond them together and the bond strength was based upon the strength of the glue. When someone looks at a glued pack sample they are looking at a perfectly glued pack at every single glue point location, applied by hand. These samples look and feel solid, but they are only samples. In reality, to maximize efficiency and minimize cost, production fill packs run through a glue application machine at high speeds and not every glue point is perfectly glued in one pass (that’s why it is important to regularly test production packs for missed glue points and mechanical properties). There is the potential for variation from pack to pack depending on the experience and capability of the worker producing the packs as well as variation from person to person on pack quality. Final glue quality will not be known until the pack has fully cured, which might be on the truck as the pack makes its way to your jobsite.
The MA process eliminates the potential for variation from pack to pack that comes from the experience and capability of the worker producing the packs and variation from person to person on pack quality. Note that the non-crushed MA cones are an engineering design feature that provides added beam strength to the packs and are not designed or intended to be crimped. These are not “missed crimps.” Also note that because they are mechanically assembled instead of glued, there will be a little movement in the packs. This is by no means an indicator of reduced strength (as some claim). Testing has proven that the bonds remain intact throughout any temperature extreme and for the useful life of the PVC material. When the MA pack is completed you will notice some movement in them when you apply a shear force and try to rack the pack. This slight movement actually makes these packs less prone to popped joints during rough handling than glued or heat-welded packs.
The strength of the MA bond is extremely robust and more than capable of withstanding rough handling during transport and installation and able to hold together over time when installed, proven by the decades of successful installations worldwide. MA packs have been in use for over 15 years in the most extreme applications. Brentwood regularly has 0.00% claims year over year for MA pack failures during shipping, handling during installation or warranty claims after the fill is installed in towers. While placing a glued pack next to an MA pack and jiggling them may make for a good selling tactic to scare owners, there’s no validity in the claim. Simply asking any manufacturer to provide test results on crush strength of a fill pack should alleviate any concerns of pack strength.
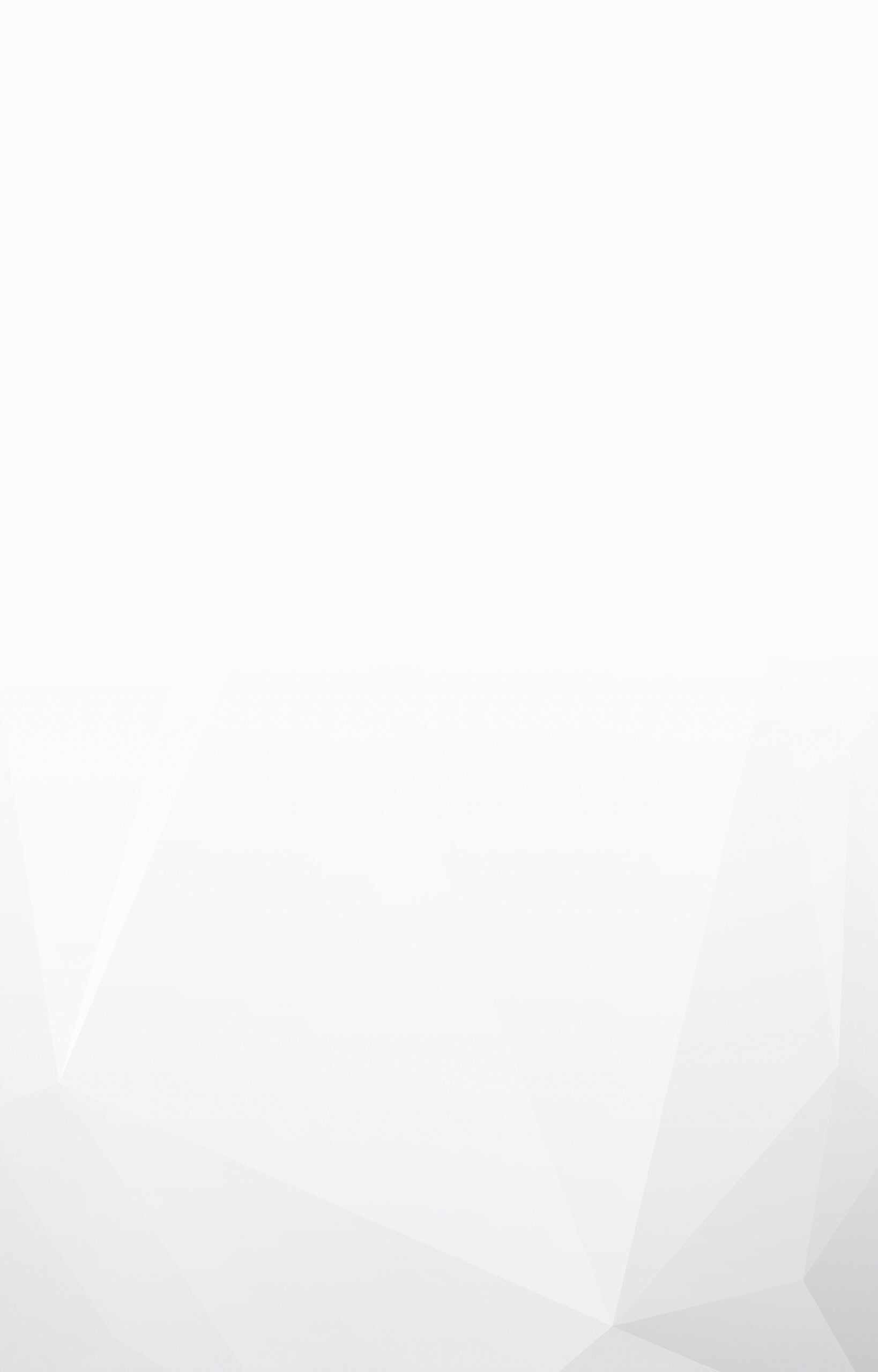