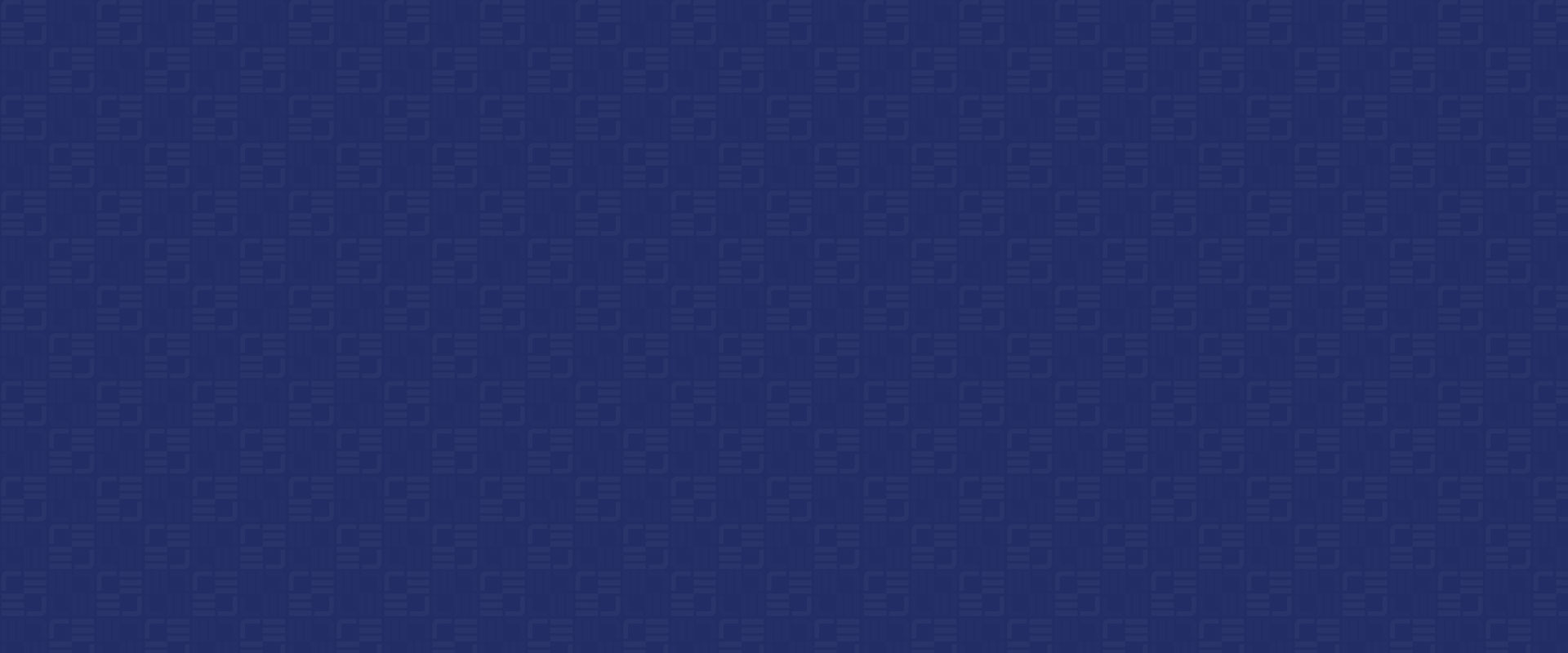
Categories: Cooling Tower.
When purchasing film fills, it is important to understand the difference between before-forming and after-forming thickness as well as the quality of PVC being formed. During the thermoforming process, the PVC sheet is warmed in an oven and then stretched over the tooling to make the fill corrugations. The stretching process thins the material, especially at the top of the flute’s sidewalls. Because of this, the after-forming sheet thickness can be more than 50% thinner than the original PVC sheet before forming.
The diagram above shows how a 15-mil before-forming PVC thickness can actually cause the sheet to get as thin as 6 mils, in some areas, after forming. To assure that the PVC withstands heavy-duty applications, fill manufacturers should specify fills by nominal, after-forming gauge. So, if 15-mil material is required for a specific project or application, the fill thickness will be specified as “15 mils nominal, after forming.”
Many manufacturers simply utilize heat and vacuum to form the sheets as this is the least costly technique and the most rudimentary to operate and maintain. However, this manufacturing process does nothing to address the uniformity of sheet thickness. Certain measures can be taken to ensure consistency in material thickness. Brentwood’s cooling tower products, for example, are manufactured using inline vacuum and pressure forming machines. These machines range in size depending on which products they produce. The tools on the machines are paired with match-plugged pressure boxes to maximize the uniformity of material distribution and minimize variation in gauge throughout the sheet.
Adding positive mechanical and air pressure to the vacuum process does increase the cost of thermoforming, however, it allows for the production of much more precise and uniform products. By manufacturing at the highest level, this assures that every product run is consistent and allows for very tight tolerances and optimal precision of the finished product.
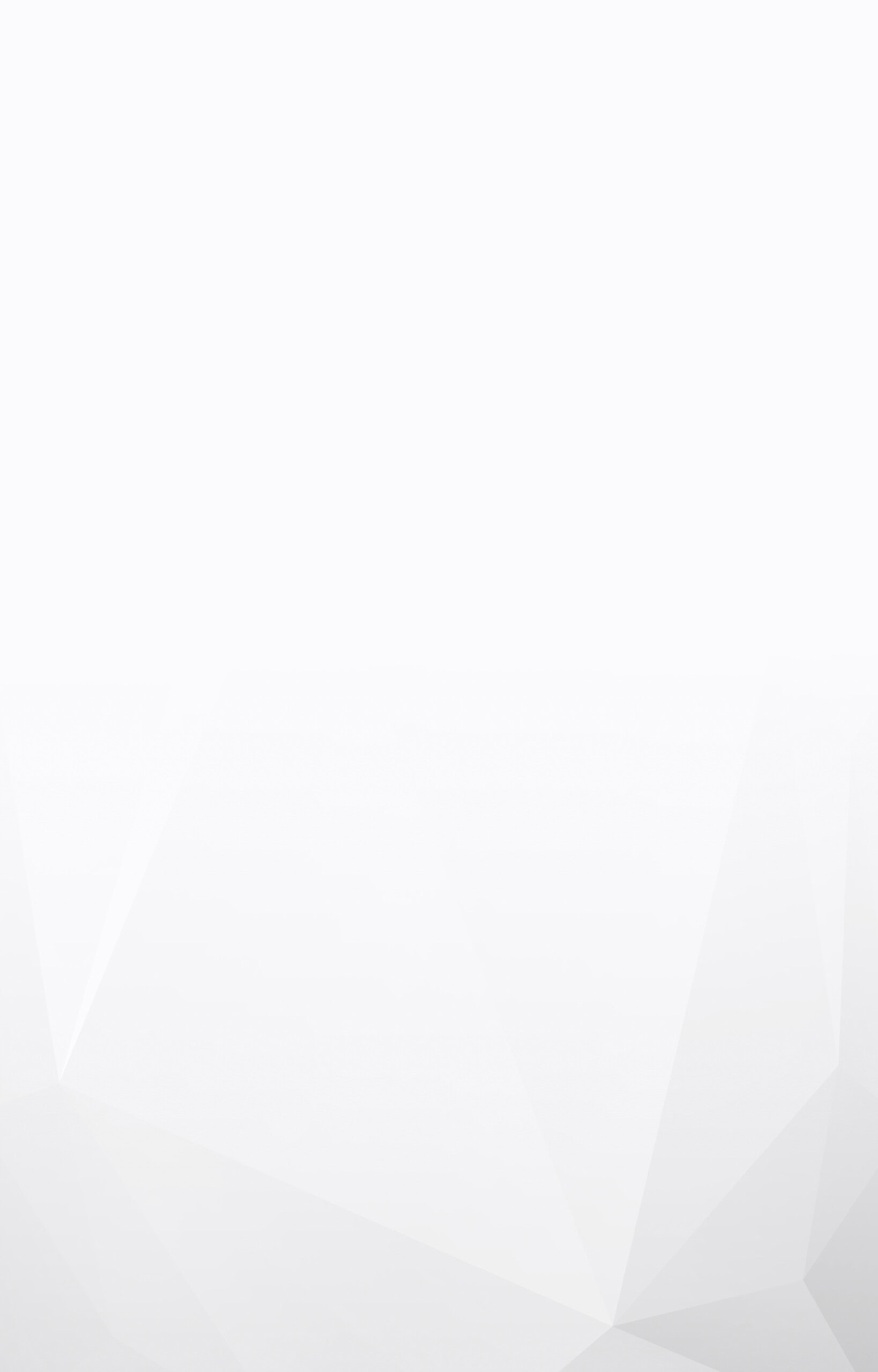