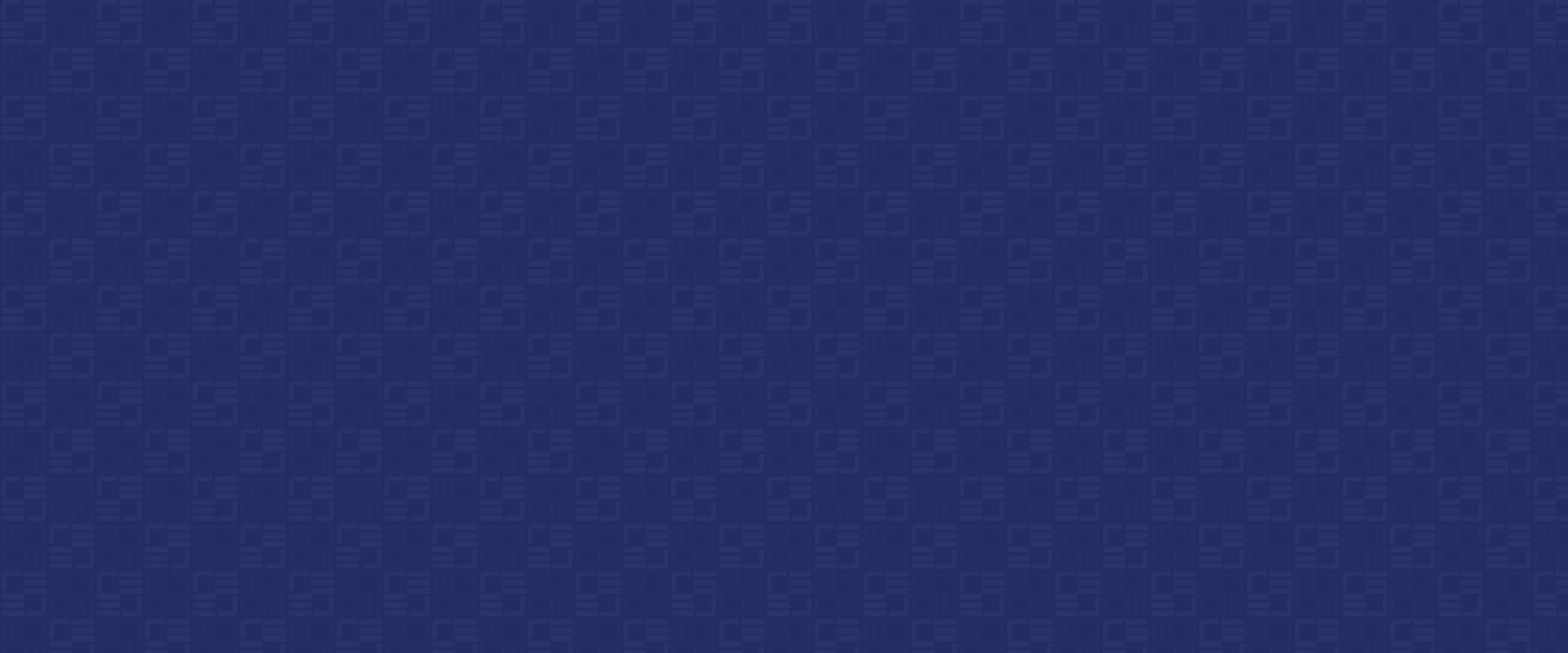
Categories: Cooling Tower.
When evaluating which heat transfer media to install in a crossflow cooling tower, most options can be classified as a film fill or splash media. Film fill, either hanging sheets or bottom supported packs, are typically found in small to mid-size crossflow towers with good water quality. Whereas splash media, such as splash bars, are historically used in larger field erected crossflow cooling towers with poor water quality. Let’s focus on towers that are originally designed with a film fill that has quickly fouled, lost thermal performance, and requires replacement. Tower owners can simply swap the fouled fill with a direct replacement, but this course of action will most likely yield the same result and again require replacement after a short period. Instead, a fouling resistant alternative to film fill should be considered. Increased fouling resistance commonly equates to lower thermal performance; however, the extended useful service life of the media may quickly counter the initial thermal derate. In the crossflow space, Brentwood offers three main fouling resistant options that can be considered – traditional splash bars, TurboSplash, and HTP25.
SPLASH BARS
The most fouling resistant media for a crossflow cooling tower is splash bars. Splash bars are installed in a uniform grid configuration either parallel or perpendicular to the incoming airflow. Splash bars create a surface for water droplets to impact, causing larger droplets to break into many smaller droplets with higher overall surface area, thus increasing the area for air-water interaction. While splash bars are one of the oldest methods of creating increased cooling potential within a cooling tower, they have experienced significant improvements over the years. Brentwood offers a wide range of various splash bar profiles; however, the latest generation of splash bars is SpiraBar, a pulse-extruded, tubular profile splash bar with diamond shape openings. SpiraBar is manufactured to length in high-density polyethylene or fire-retardant high-density polyethylene. Available in multiple shapes and sizes, SpiraBar provides improved thermal performance over legacy splash bars in extremely dirty water applications.
MODULAR SPLASH FILLS
Two modular fouling resistant alternatives to traditional splash bars are TurboSplash and HTP25. TurboSplash is a high-performance modular splash fill that has been successfully installed in crossflow cooling towers with highly contaminated water supplies, such as those found in the power, refining, petrochemical, steel, chemical, pulp & paper, and food processing industries. TurboSplash packs consist of injection molded polypropylene panels that are assembled into hinged bundles allowing for optimized shipping and installation. Available in either a 4” (SF100) or 6” (SF150) panel-to-panel spread, each panel utilizes thirty-eight angled paddles to encourage turbulent air and water mixing for efficient heat transfer. Each TurboSplash panel has integrated molded-in saddles for positive alignment and secure installation to intermediate pipe supports, allowing multiple layers to be installed easily. HTP25 is another modular splash offering that has been successfully installed in small package to mid-size crossflow towers where poor water quality does not allow for effective use of traditional film fill. When evaluating the different fouling resistant crossflow media options, HTP25 will typically provide the highest thermal performance. The injection molded HTP25 sheets are mechanically assembled into fill modules. Each cubic foot of HTP25 utilizes over 3,600 drip points to provide maximum thermal performance. Similar to a standard film fill pack, HTP25 is bottom supported. This greatly cuts down on the necessary installation time as compared to a traditional splash bar. Available in either standard polypropylene or a fire-retardant polypropylene, HTP25 is an excellent alternative in applications where the circulating water has high levels of suspended solids but the tower owner requires as close to OEM design performance as possible.
While there may be an initial derate to the tower’s thermal performance compared to a traditional film fill repack, the above alternatives offer greater resistance to fouling and a longer effective service life. The table below outlines the general allowable water quality guidelines for each of Brentwood’s crossflow fill options. For support on selecting the optimal crossflow fill for your specific application, please reach out to your account representative.
1 ‘Good’ biological control means oxidizing biocide supplied continuously with bactericidal residuals maintained, with total aerobic bacteria (TAB) maximum plate counts not exceeding 100,000 cfu/ml with minimal slime formation on heat transfer surfaces.
2 ‘Poor’ microbiological control implies little or no microbiological control or control subject to severe disruption, with average TAB plate counts consistently over 100,000 cfu/ml.
3 Values listed represent concentrations of light, soluble oils. Heavy oils and greases would require a specific recommendation on a job-to-job basis.
4 Values listed require limits on the concentrations of light, soluble oils to 5ppm or less and 0ppm on heavy oils & greases.
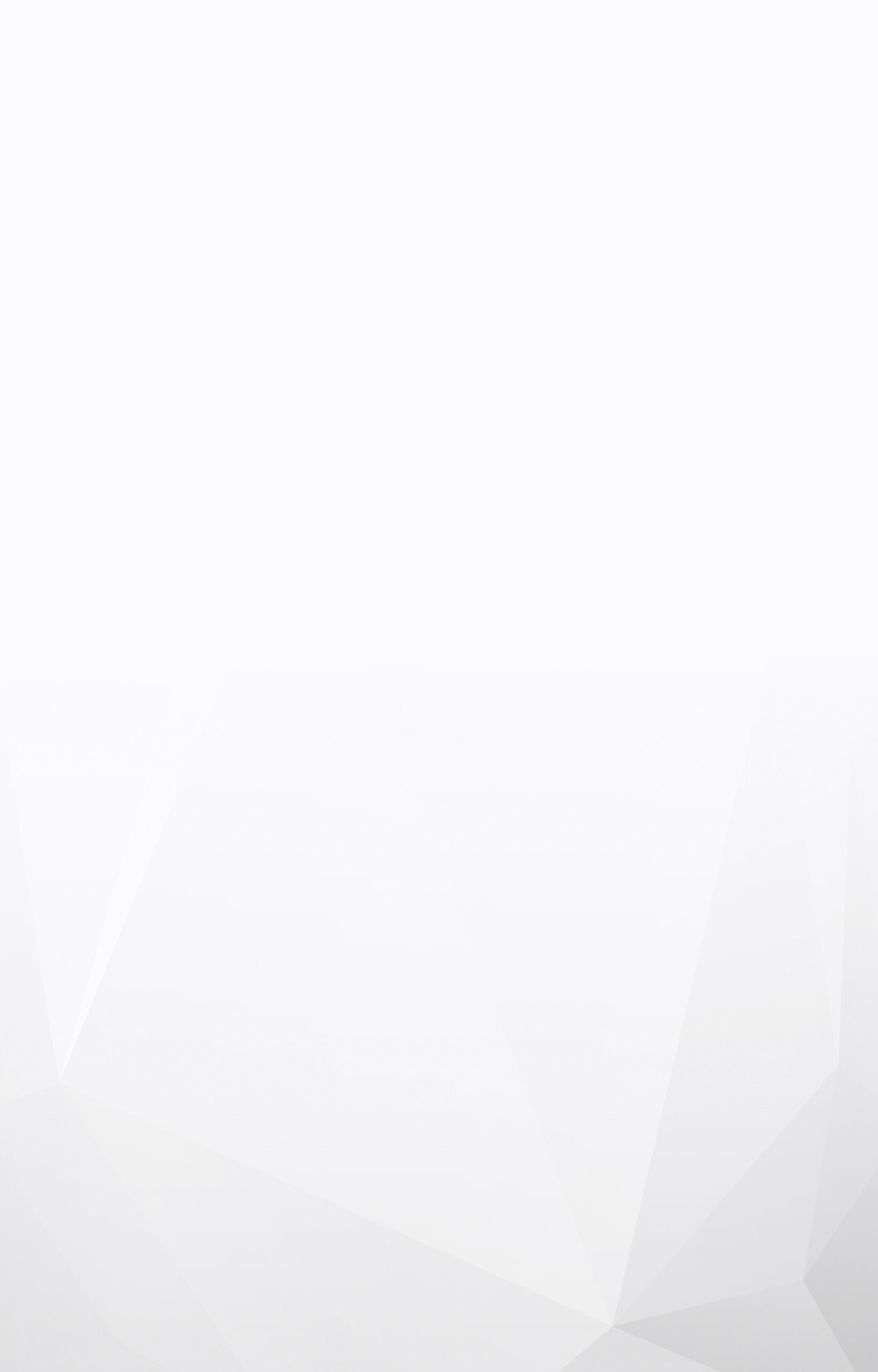