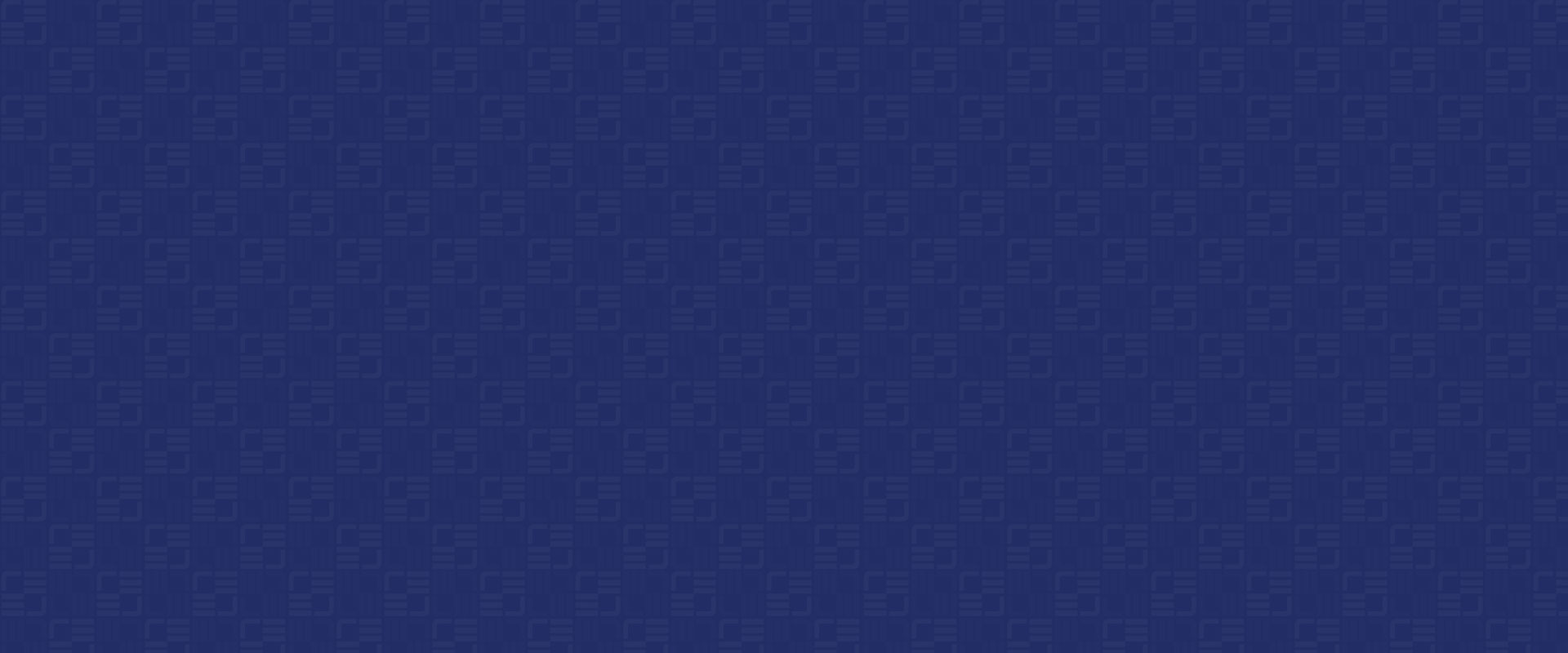
Categories: Medical.
Today, nearly 40 years later, we continue to expand our capabilities, investing in a custom Sencorp ULTRA thermoformer that will allow us to form parts at an industry-leading 72” long inline. The machine will join the eight other production lines inside our 30,000-square-foot, ISO Class 7 clean room this month.
The new Sencorp ULTRA thermoforming machine is able to accommodate parts up to an overall size of 72” x 34” x 6” and materials ranging from 0.010” to 0.080” starting thickness. This machine will produce trays in all of the common medical materials such as PETG, HIPS, PVC, PP and HDPE. It incorporates several features that will make us more efficient and allow us to offer those potential savings to our customers. The Sencorp ULTRA is loaded with features that will improve production efficiency and repeatability:
- A closed loop 7-zone inline infrared sheet temperature sensing system ensures that tooling validations are accurate, efficient, and repeatable.
- A Robotic pick-and-place system allows the machine to remove, stack, and pack product, minimizing cycle time and maximizing labor efficiency.
- Our quick change master tooling system will attach to the Sencorp ULTRA machine’s form and trim platen using Segen locks for fast and precise installations. This will reduce changeover time and setup costs, while also helping us control tooling costs for low-volume projects where the investment in a fully custom tool can be prohibitive.
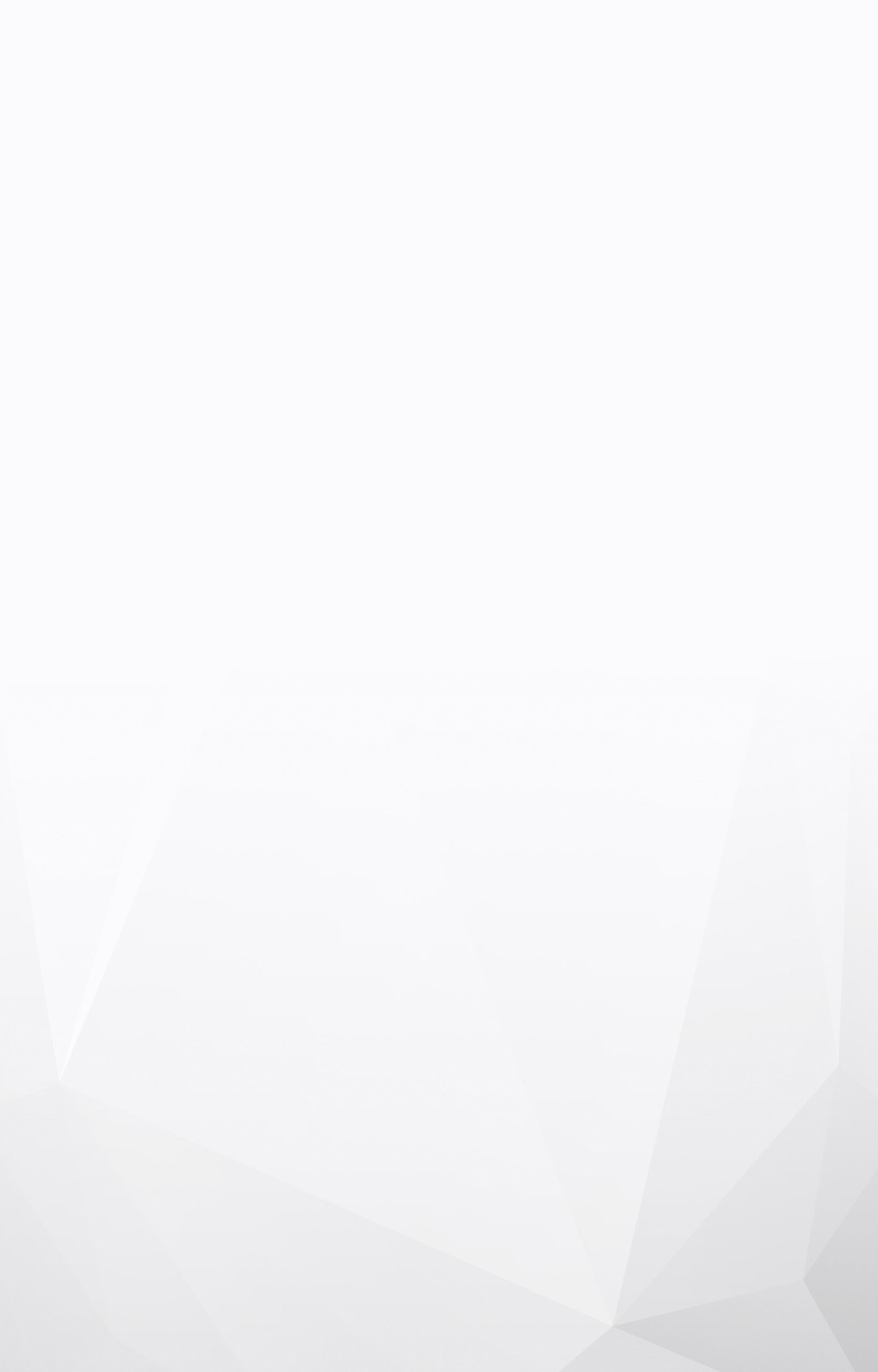