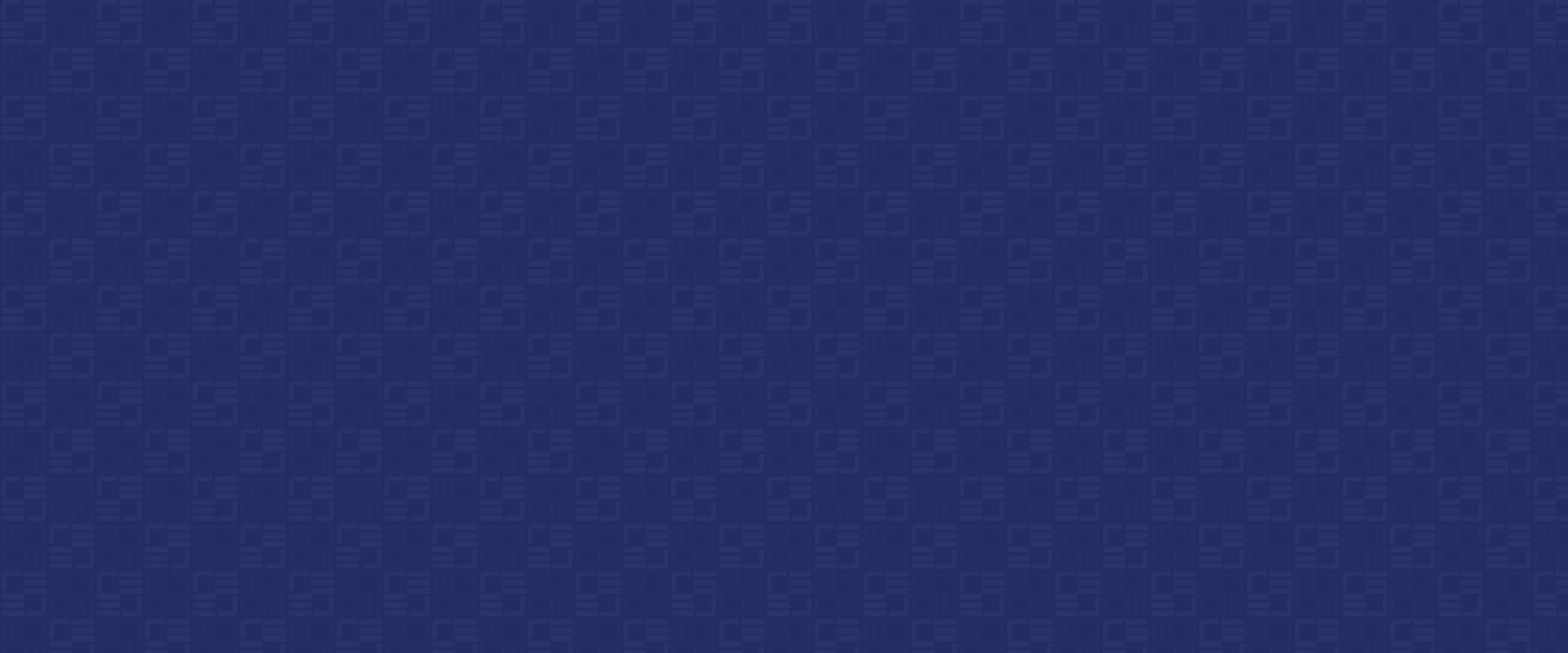
Categories: Stormwater.
Q: I see you have a 12” inlet/outlet port. Is that the only size that can be used? And is it the only way to make a connection?
A: The 12” port is a legacy offering from the inception of the StormTank Module, but the port does not restrict the pipe size that can be used, nor is it the only way a pipe can be connected to the system. In fact, the most common form of pipe connection is a direct pipe penetration, where an opening is cut into a side panel, the pipe is inserted, geotextile fabric is wrapped around the connection, and the opening is sealed. This form of connection allows for a lot of flexibility, enabling the use of almost any size pipe connection.
Q: Can I only connect to the side of the system and from only one direction?
A: No, you can also connect to the top or bottom of the Module, but with these connections the pipe diameter is limited to a maximum 10”, and you must use Brentwood-manufactured ports. In addition to the flexibility to connect from the bottom or top, you can connect to the system from any direction.
Many other linear systems, like arch chambers and pipes, limit the direction that connections can be made (only parallel to the product row). Therefore, they use header manifolds or structures to redirect the flows into the individual rows. But since the Module is an open vault with vertical sides, you can connect from almost any direction without extra products or structures.
Q: What is the maximum pipe size that can be used?
A: The maximum pipe size is based on the height of the Module specified. The Module is comprised of a top and bottom platen, separated by vertical support columns. These platens are each about 2.0” thick, meaning the potential opening is reduced. To account for this, the common recommendation is to leave about 3.0” of height from the invert and top of the Module. This means, on a 36” Module, the maximum opening that can be cut into a side panel is about 30”. (One caveat: every type of pipe has a different wall thickness that could be a limitation to the available height).
Q: How do I connect a pipe that is larger than the height of the Module?
A: There are only two ways to connect a larger diameter pipe. The first is by using a header manifold that divides the large pipe into multiple smaller diameter pipes. The second way is to use a concrete structure, like an inlet, and directly adjoin it to the Module. This structure can then have an opening, or multiple openings, cut into it and Modules directly abutted, allowing for a larger potential opening than a direct pipe connection.
Q: What kind of pipe material can be used?
A: Plastic, metal, or concrete pipes can be used to connect to the StormTank Module system. However, it’s important to keep in mind that not all pipes are equal. Each type of pipe has a different wall thickness, and some may have corrugations that need to be considered when sizing and installing.
Plastic (HDPE, PP, PVC) pipe is the recommended material for connecting. This material is the easiest to work with and is most similar to the material the StormTank Modules are made of. Metal pipes are the second-best option, but these are less structurally sound and can rust over time, so they should be selected carefully. Concrete pipe is the least recommended pipe material because it is heavy, has thicker walls, and it’s more difficult to modify the length. Another very important consideration when it comes to concrete pipe is that the diameter listed is the interior diameter, and therefore, you must account for the 3” wall thickness. So, if we were to use an 18” StormTank Module as an example, your pipe is now limited to 6” for direct pipe penetration and anything larger would have to be abutted, creating the potential for movement and material migration into the system.
While those are the most common questions we hear from engineers and contractors, it doesn’t mean they’re the only ones. Brentwood maintains a technical design assistance team that can answer your questions any time. Whenever you are designing or installing a system, feel free to reach out to us with your specific project questions and concerns. We’re here to help!
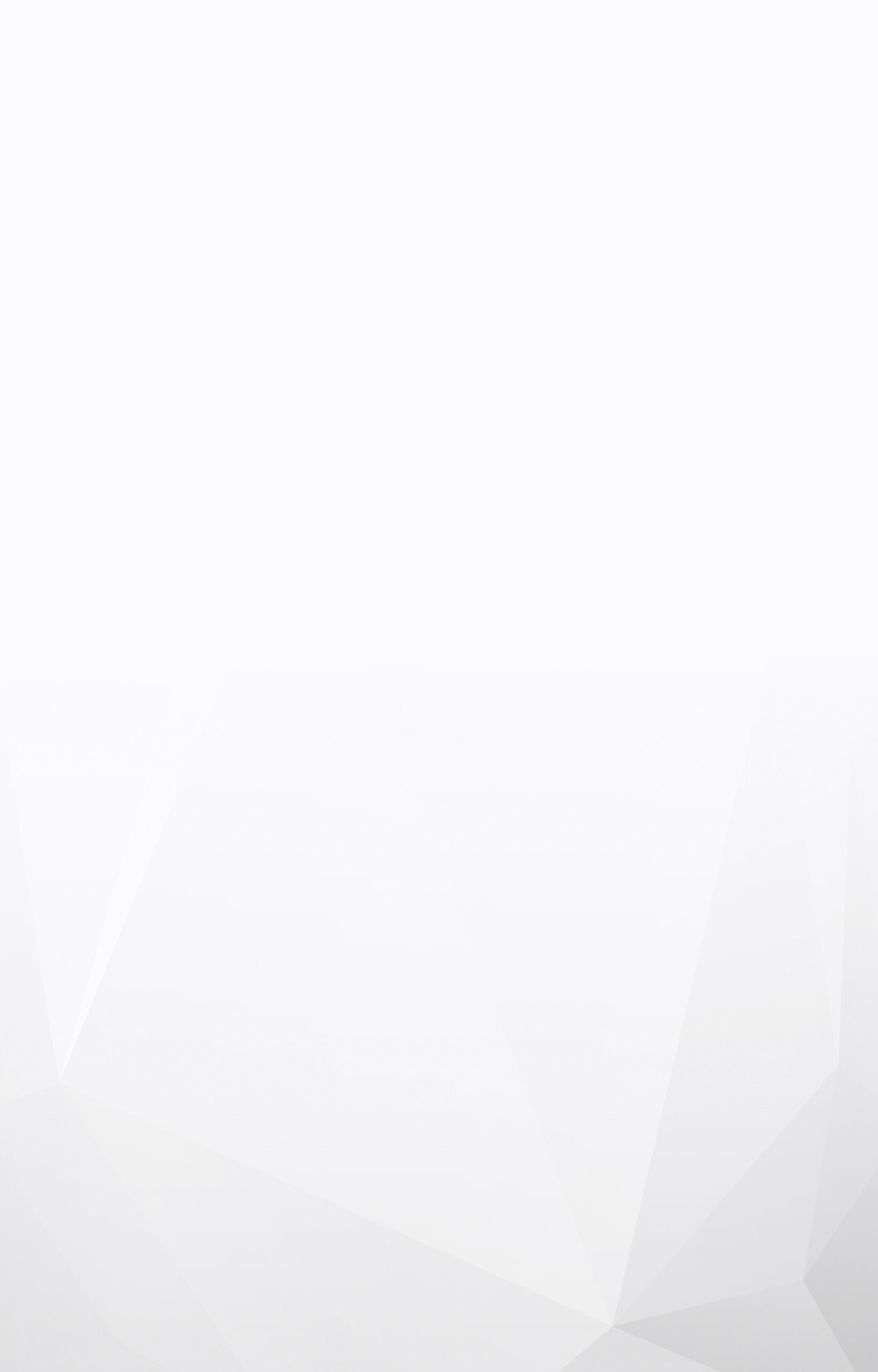