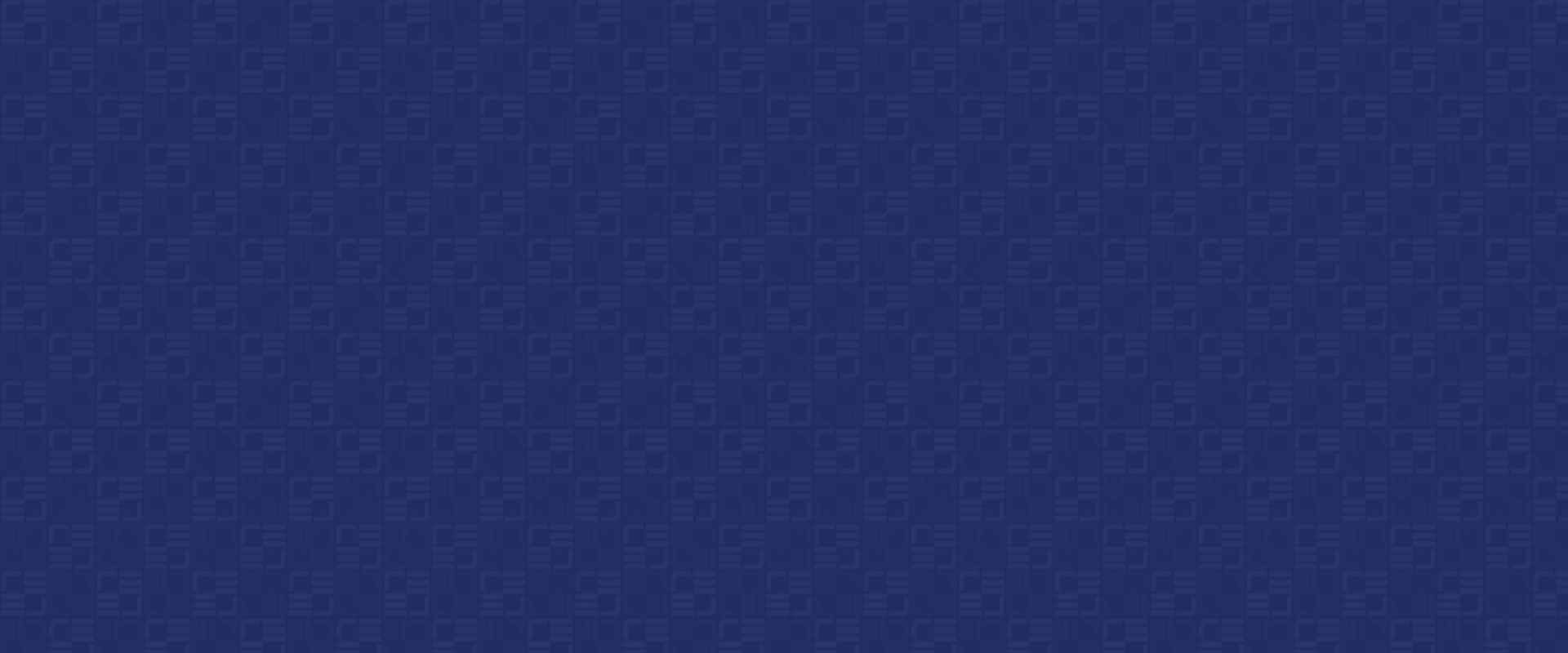
Categories: Transportation.
Heavy Truck
For many years, Brentwood thermoformed interior cab parts for Mack Truck, Inc.’s cab-over-engine truck, but this changed in the late 80s when highway rules were adjusted. The updated rules allowed for extended vehicle length and included both splash and decibel requirements. Brentwood worked with Mack to develop a solution for their new line of trucks that would allow them to be compliant with regulations. We designed and manufactured splash guards, made from high-molecular-weight-polyethylene (HMWPE), to prevent the splash coming off the tires from hitting the windshield and muffle the engine sound.
By the early 90s, Brentwood was making large exterior parts for the heavy truck industry. The first pieces included wheel wells and light fixtures, which can still be seen on some trucks today. As the business grew, it required the addition of 30-40 router stations filled, all utilized by employees cutting out truck parts. In 1994, Brentwood also acquired several CNC trimming machines so that employees could transition to operating machines and productivity could be drastically increased.
A pivotal moment for Brentwood’s heavy gauge business was creating the first plastic truck bumper for Mack’s Pinnacle highway vehicle in 2006. A special machine was purchased for this purpose and enables us to form thermoplastic olefin (TPO), a material inherently difficult to form due to its narrow temperature band. The machine also gave Brentwood the ability to thermoform other large parts and expand its business in the automotive and mass transit sectors.
Today, Brentwood continues to work with the Heavy Truck Industry, including Mack Trucks and Volvo Trucks.
Rail
Brentwood’s first big break in the rail industry was the Long Island Railroad project in the 1970s. A relationship with a local company, General Seating, led to Brentwood supplying thermoformed parts for railcar seats and interior panels. We were eager to help in this endeavor and expand our knowledge and expertise to the rail industry. Brentwood successfully formed the parts, which were used in the M1 Long Island Railroad cars, as well as incorporated into some Septa railcars.
In the early 1990s, Brentwood built on previous success in the mass transit industry by taking on the development of parts for Amtrak. We were invited to the Amtrak facility, along with four other thermoforming companies, to present our case for forming the interior replacement parts. Since Amtrak’s previous supplier went out of business and no tool could be obtained, new tooling was developed in-house. The effort made Brentwood the only viable supplier, gaining all of Amtrak’s replacement part business.
Brentwood continues to work on rail projects today and seeks to expand the business through commitment to the IRIS quality standard and driving towards the most competitive rates in quality thermoforming.
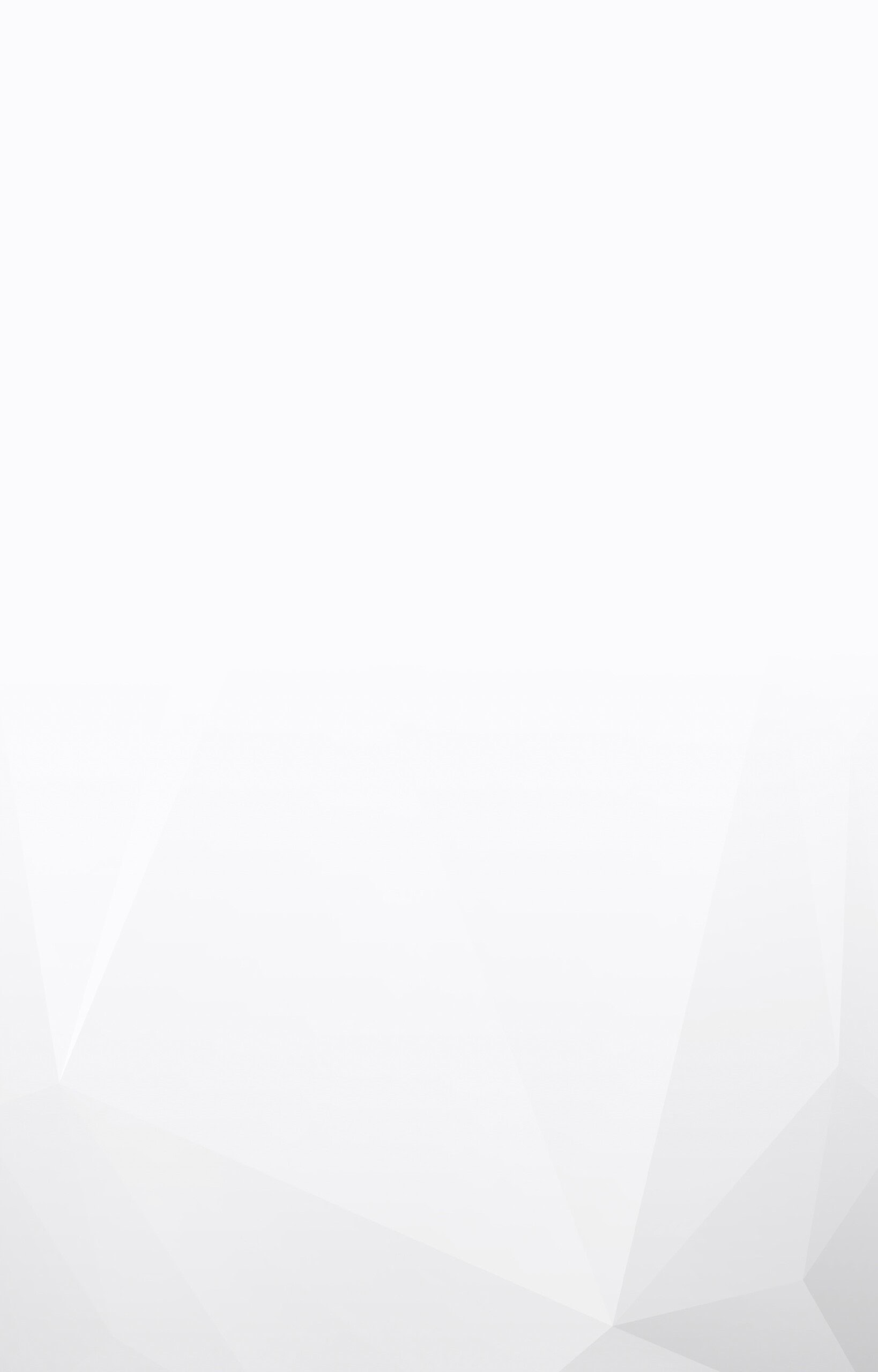