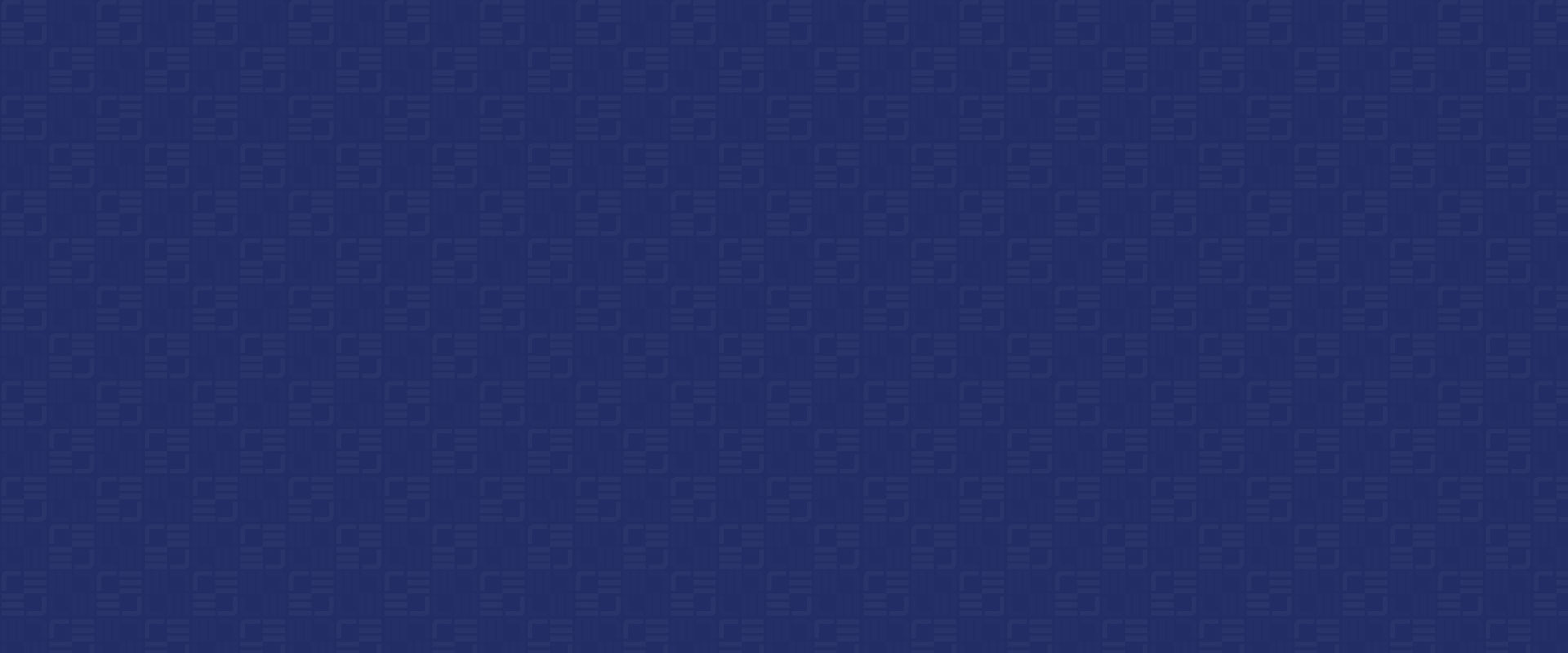
Categories: Water & Wastewater.
The main purpose of a trickling filter, or biotower, support system is to support the media above. But did you know that supports also play a crucial role in successful system operation and performance? Understanding the importance of support systems, the benefits and limitations of manufacturer-supplied systems, and what pertinent design information to be cognizant of will help expedite a trickling filter project and avoid installation headaches down the road.
Process Considerations
A support system is one of three primary players in a trickling filter underdrain system. Underdrain systems also serve to promote
Conveyance: A support system should be adjustable to accommodate the floor slope required to convey effluent in a trickling filter. In circular filters, channels typically run through the center of the filter. However, other designs exist.
Convection: Most trickling filters rely on natural convection to supply aeration. In this process, the temperature difference between the interior and exterior of the filter drive air into the filter. A supplementary fan system may be used when loading is high or when the interior/exterior temperature differential is too low. Brentwood has observed beneficial results both in increasing organic loading and treatment efficacy for filters with increased underdrain height. For trickling filters undergoing a retrofit, utilizing a manufacturer-supplied support system and increasing underdrain height may help meet more restrictive effluent limits and increase treatment capacity. Be aware that an inadequately tall underdrain system can cause stagnation and impend airflow.
Existing rock filters, especially shallow filters with low underdrain heights, are not optimal for trickling filter performance. As plastic media increases the treatment capacity of an existing rock filter, it is highly recommended that the designer also consider whether the underdrain system will allow enough aeration to accommodate an increase in loading. Estimations for aeration supplied as well as recommendations for minimum underdrain heights are located in the WEF Manual of Practice 8, 4th edition, Aerobic Fixed Growth Reactors. Brentwood can also supply this information upon request.
Upgrading Existing Support Systems
In the 1980s and 1990s, most support systems consisted of either cast-in-place or precast concrete beams. These beams are usually 6” to 8” wide and may or may not have drainage slots (Aerobic, 156-157). The spacing of these beams varies, but a 2’ on-center spacing is typical (Aerobic, 156-157). In the early 2000s, manufacturer-supplied support systems became more common for retrofits and new builds due to their ease of installation and lower cost. The best improvement method ultimately depends on the type of trickling filter and its current support system.
For shallow filters with a tile support system, it is recommended that the support system be replaced with a manufacturer-supplied system due to the low underdrain height commonly found in these systems.
For filters that have concrete posts and beams, it is recommended that fiberglass (FRP) grating be installed atop the concrete beams to improve drainage. Wooden beams should be replaced with either a manufacturer-supplied support system or an entirely new support system.
The condition of any existing concrete should be carefully evaluated at the onset of the project. Debilitated concrete will render any support system useless. Note that condition cannot be evaluated by the manufacturer, even in situations where a P.E.-certified structural design is provided.
Manufacturer-Supplied Support Systems
While exact layouts and dimensions vary, all manufacturer-supplied support systems consist of a similar design. These systems
Typically, the pier support system must be 9” to 42” in height. The minimum height requirement is also important to ensure proper aeration to the filter. Pier systems exceeding 42” in height can be provided, but require special design.
Support systems must be designed to support the weight of the media, biomass, and water with appropriate safety factor. This load should be incorporated into the specification. Design loading is estimated based on studies provided by DOW Chemical Company, where modules were weighed after operation. Design load is based on the height of the media. The taller the filter, the greater the weight for a system to support.
Most manufacturers use third party vendors for certain components of their support systems, like FRP grating and fasteners.
FRP grating is often the governing factor for design, as most pier support systems can handle design loads much higher than the grating. FRP grating is typically designed to withstand a certain design load. These design loads should be incorporated into the specification. Typically, a 2” high by 1’ or 2’ wide grating is supplied at lengths most economical for cutting.
A resin coating should be applied to the FRP grating to withstand corrosive environments found in trickling filters. Resin offerings for FRP gratings usually fall into one of two categories for trickling filter applications:
- Polyesters. Polyesters are fire retardant with moderate corrosion resistance. This resin is suitable for most municipal applications and non-corrosive industrial applications.
- Vinyl esters. Vinyl esters are fire retardant with excellent corrosion resistance. This is suitable for corrosive industrial applications.
Providing a P.E.-certified structural design should be simple for a supplier. A variety of third-party structural consultants can be contracted for a nominal fee. Manufacturers should be familiar with providing P.E.-certified designs, as structural consultants will require information from the supplier. It is possible that test data may need to be provided by the supplier, as well.
Support systems supplied by Brentwood are laid out in a grid. Spacing from pier to pier is typically 2’x 3’ or 3’x3’ depending on trickling filter height. FRP grating is secured on top of the pier system. For basins with suitable concrete beams, FRP grating is secured to the beams. Depending on the loading to the filter, grating is supplied with either 100% or 50% coverage. See below for a few examples:
Support System Installation
Support system installation first requires creating a grid using chalk lines and marking pier locations on the basin floor. Bases are leveled using Brentwood’s design that allows for easy field adjustment to account for floor slope. In non-seismic zones, powder actuated pins can anchor support bases. PVC pipe lengths are measured and cut. The remainder of the pier system is then assembled and FRP grating is secured to the top.
Site Conditions
It is very important to establish whether a trickling filter falls within a seismic zone early in the design process. Seismic zones require special considerations. Both the risk category and site class must be established for proper design. A seismic zone will require special anchoring and will affect the anchors chosen and installation time required. In some cases, it may be prudent to perform a P.E.-certified design prior to project bidding to firmly establish specification requirements.
Trickling Filter Analysis Checklist
Trickling filter support systems are important for both the integrity of the filter and its treatment performance. The earlier a support system is analyzed, the better the results and the more cost-efficient the solution. This includes bringing manufacturers on early in the design process by sharing support system drawings, site conditions, and project goals. Depending on the situation, a manufacturer-supplied support system can be a good option, but any retrofit situation should be approached on a case-by-case basis. Refer to our checklist below as a basis for analyzing support systems and what to include in a specification:
References
Water Environment Federation. (2000). Aerobic fixed-growth reactors.
Creative Pultrusions, Inc (2004). The Pultex Pultrusion Design Manual.
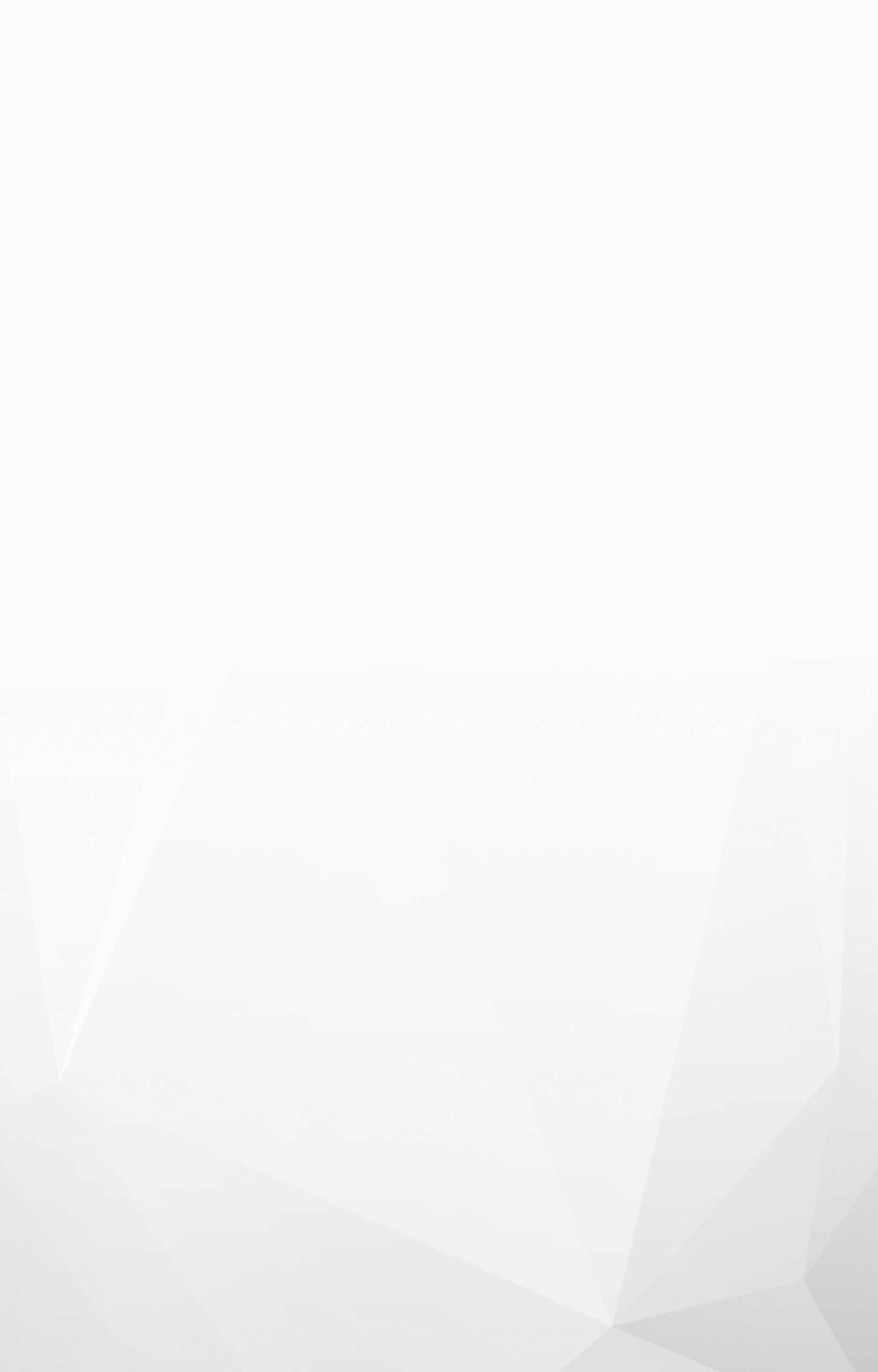