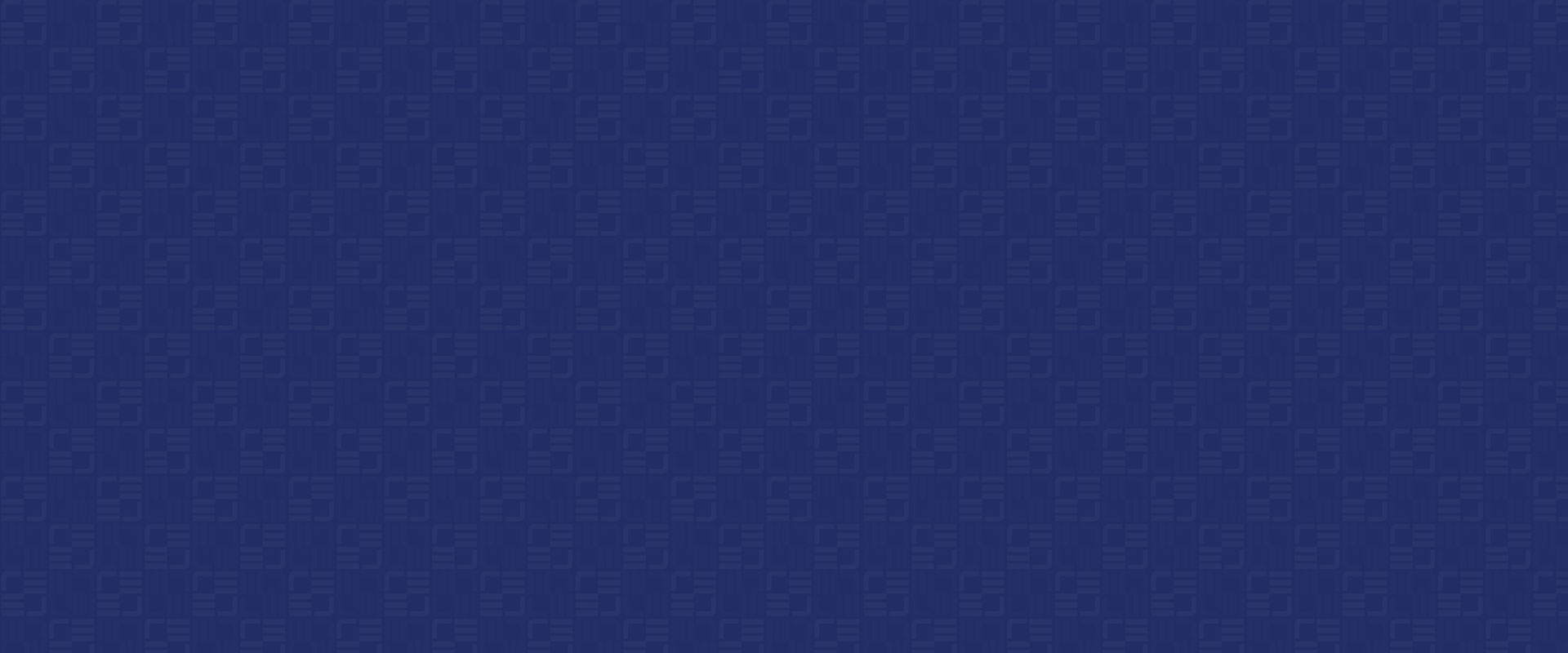
Categories: Water & Wastewater.
When choosing media for fixed-film applications, typical options include small, floating biomass carriers (moving bed systems) or structured-sheet PVC modules fixed in the tank (fixed bed systems). Several companies manufacture moving bed systems using a variety of floating biomass carriers and media retention systems. Brentwood offers the structured-sheet media modules used in the AccuFAS fixed-film system.
Fixed and moving bed systems have several features in common:
- Provide a surface for nitrifying bacteria growth.
- Provide similar levels of treatment for same basin size.
- Operate as single pass without return solids as a moving bed biofilm reactor (MBBR) or fixed bed biofilm reactor (FBBR) process.
- Operate with return solids as an integrated fixed-film activated sludge (IFAS) process.
- Easily retrofitted into existing tanks.
However, there are significant differences between moving biomass carriers and structured-sheet modules that should be considered when evaluating these fixed-film systems. The top five are:
- Basin Geometry: Moving bed systems are typically limited to a 2:1 length to width ratio to prevent media from bunching up at the outlet. Fixed bed systems have no limitation on the tank geometry and work well in long, plug flow configurations.
- Media Retention and Headloss: Submerged screens are required to retain biomass carriers in the aeration basin for moving bed systems. These add headloss, which adversely affects the plant hydraulic profile. Washouts and catastrophic loss of media are possible. On the other hand, structured-sheet modules are secured in the aeration basin using supports and restraints, preventing loss of media with no additional headloss.
- Surface Area and Kinetic Rates: Moving biomass carriers are available with specific surface area from 164-365 ft2/ft3 (500 to 1200 m2/m3). Structured-sheet modules’ specific surface area varies from 50-96 ft2/ft3 (164-315 m2/m3). The kinetic rates (pounds removed per square foot per day) for structured-sheet modules are greater due to optimized mass transfer.
- Aeration and Mixing Requirements: Coarse bubble diffusers typically provide process aeration and mixing of the media for moving bed systems. Structured-sheet modules work with fine or coarse bubble diffusers, typically sized for process air only, and do not require additional air for mixing.
- Total System Cost: A useful comparison between fixed and moving bed systems cannot be made on the basis of a single parameter, such as specific surface area, kinetic rates, or media cost. Fair evaluation requires comparing the total installed capital AND operating costs.
These five differences between fixed and moving bed systems will be discussed in further detail as individual blog posts over the new few weeks. Please check back for more info, comment below, and/or reach out to Brentwood with any questions at accufas@brentwoodindustries.com.
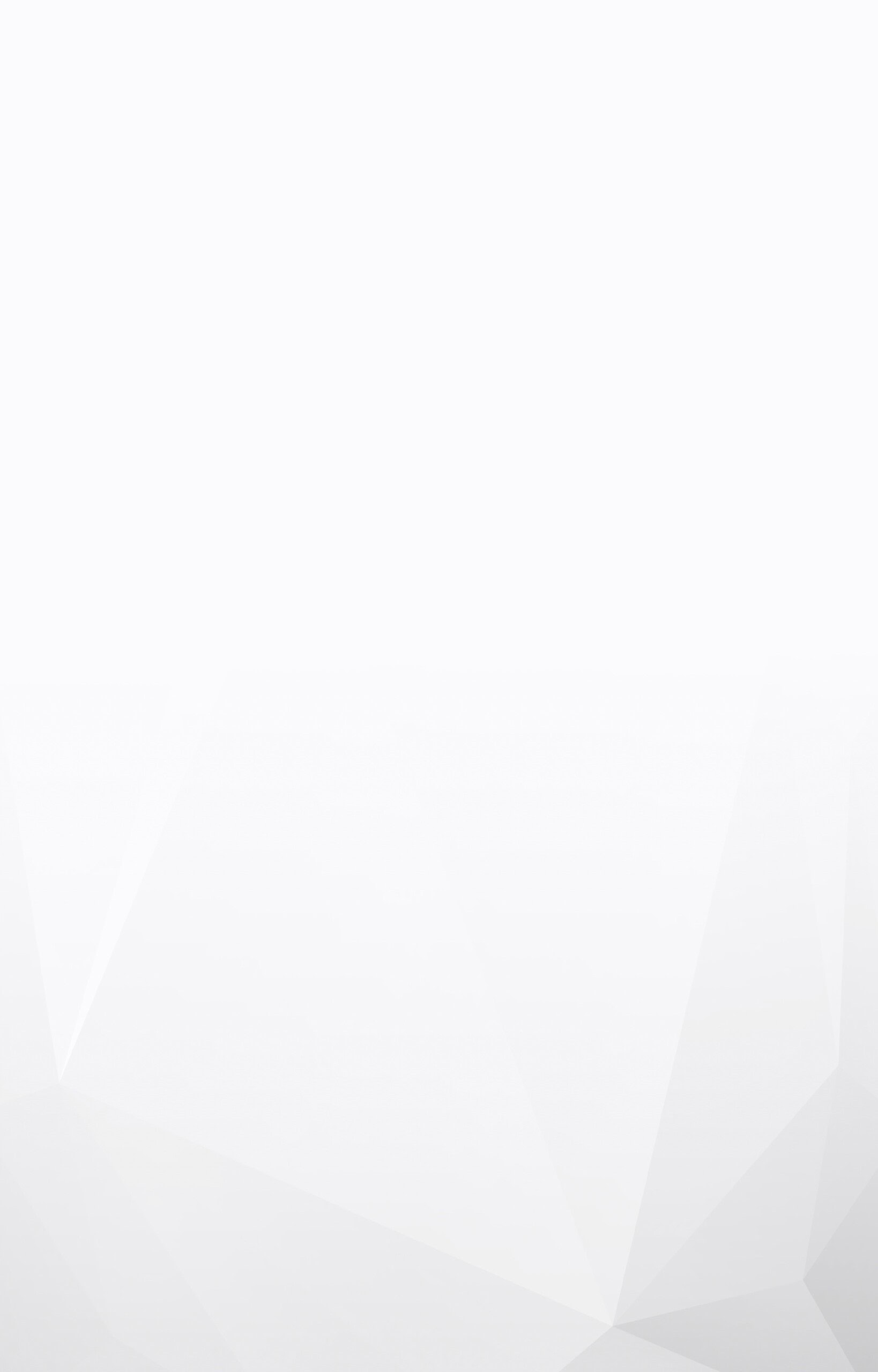