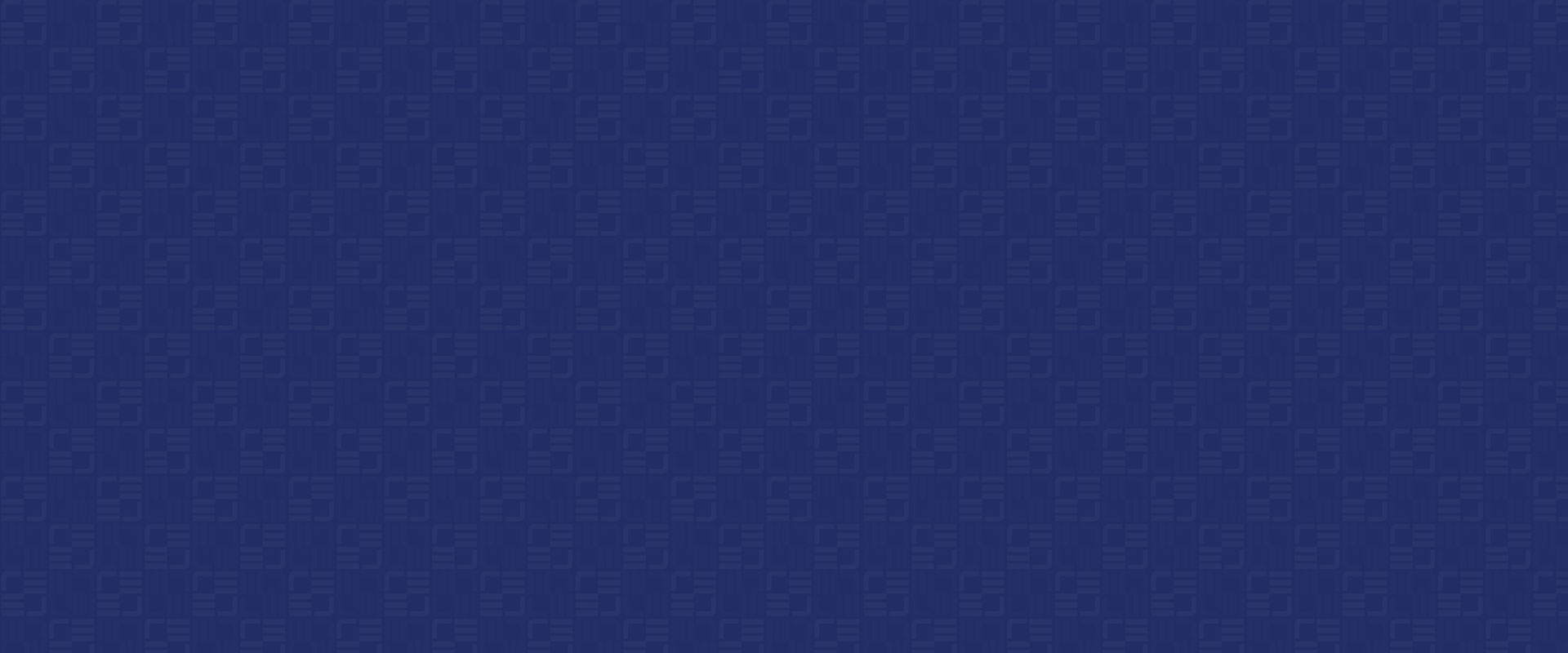
Categories: Water & Wastewater.
What should you consider when planning to replace the flights in your rectangular clarifier? Flights are also known as scrapers, c-channels, flight boards, drag flights, and sludge pushers. Regardless of what you call them, they serve the same purpose. Flights convey settled solids to a hopper or collection pit and push surface debris into a scum removal device in a straight-line clarifier system. Although flights may all seem the same at first glance, there are some key characteristics to think about when evaluating which type you may need for your chain and scraper system.
The Evolution of Flight Scrapers
To better understand what aspects to look for in a flight, it’s important to learn how they evolved into their modern-day configurations. The first flights introduced in 1929 were made of redwood or Douglas fir. As wood is buoyant, these sludge scrapers required weights to ensure that they stayed at the bottom of the tank. They employed metallic wear shoes, ran on steel return track and floor tee rail, and moved with steel collector chain that articulated over cast-iron sprocket gears. While this equipment was heavy duty, it was also plain heavy. The weight of the equipment, coupled with metal churning on steel surfaces, created high friction. These systems required large drive units and consumed excessive amounts of power. The sheer weight of the equipment made periodic maintenance a challenge. In addition, the metallic components would eventually rust and corrode, shortening system lifespan.
It wasn’t until the late 1970s when manufacturers began producing lighter-weight plastic alternatives in rectangular clarifiers. New systems emerged with polymeric collector chains, nonmetallic sprockets, and UHMW-PE wear strip to reduce friction and weight. Wood flights were also replaced by fiberglass (FRP) reinforced plastic c-channels. Most suppliers of these revamped systems retained the steel head and idler shafting and converted the other in-tank components into engineered plastics.
Polychem (formerly The Budd Company) went one step further in 1982 by introducing the first 100% nonmetallic chain and flight system. This system featured a telescoping fiberglass head shaft and cast nylon idler stub shaft. The newly-added fiberglass flights proved to be non-buoyant, lightweight, and more corrosion resistant. These flight profiles featured a built-in scraper lip and were easier to install and maintain than their predecessors. As FRP scrapers were less expensive and comparable in size and strength to wooden scrapers, c-channel nonmetallic flights became the industry standard.
Top 5 Flight Considerations Before You Buy
1. Fit
While this one may seem obvious, how existing flights fit in a system is sometimes overlooked. It is imperative to know your existing flight dimensions before specifying or buying new ones, especially if you plan to retain any existing components and their locations.
For example, if your existing flights are 3” wide by 6” tall c-channels, and you are not relocating the lower idler shafting or sprockets, it would be foolish to purchase or specify a 3”x8” tall flight profile. The larger flights would be too tall to articulate around the idler sprockets and would catch on the concrete floor and possibly the underside of the deck when skimming surface scum on the return track.
Conversely, if you replaced 8-inch-tall flights with 3”x6” scrapers (still maintaining shaft locations and sprocket sizes), the new flights would not adequately convey all of the sludge at the bottom of the floor, and may not be tall enough to adequately skim the water surface. Should you make one of these mistakes, you would either need to purchase the correct profile size or make significant changes to your shaft locations, sprocket sizes, or potentially need to remove concrete from the underside of the deck.
2. Buoyancy
Buoyant flights are not ideal. If a scraper flight is buoyant, it cannot effectively push sludge or scum – its sole purpose. Buoyant flights also risk floating up to a catch point and damaging the flight or causing a crash. A buoyant flight may require additional weights which can come loose, rendering the flight buoyant, and may add significant weight to the flight. This further complicates installation and handling.
In addition to wood flights, you may also experience buoyancy issues with fiberglass flights that feature a box or closed end. Closed flight profiles can allow sludge to become trapped in the scraper and turn septic. Septic sludge disturbs the normal sedimentation process, is more corrosive, and can be more difficult to pump and dewater than normal sludge. Closed profile flights may require end capping, weights, large holes, or fillers to prevent buoyancy and septic concerns.
3. Price
Flights are, at minimum, the third highest cost impact to a standard chain and flight system. As tank width increases, or as you require heavier duty flight profiles, flights can easily become the highest cost impact. Take a look at the respective percentages of total system cost that flights can take up in these scenarios:
Since flights can significantly impact the cost of a scraper system, it’s important to ask yourself: Will future process changes at the plant require a heavier duty flight? Are my current flights inadequate and require upgrading to a stronger option? Is it cost-effective to buy more expensive flights now and get longer life out of the flight?
While your specific tank dimensions will most likely determine which flight profile you will need, here are some factors that impact flight costs:
- The type of resin used with the fiberglass and percentage of fiberglass used.
- The complexity of the profile can impact the pultrusion speed of the flight.
- The number of holes, notches, and machining cuts required.
- The number of molds used to run the specific flight profile.
- Quantity of flight run vs. machining from stock.
- Hardware type and accessories (squeegees, end wipers, wear bars, etc.).
4. Deflection
The most important consideration when choosing a new flight profile is the amount of deflection that exists. The goal of an efficient flight is to minimize deflection and maximize stiffness. Too much flight deflection is not always the cause of a tank failure. However, deflection can adversely affect other components and lead to system issues. It’s imperative that a flight is suitable for the application in terms of pushing sludge and minimizing overall flight deflection due to gravity.
Deflection is affected by a few things: the flight profile and its material properties, the width of the tank (flight span), sludge loading, and how and where the scrapers are supported on the return track and floor. There are two types of deflection to be cognizant of:
- Horizontal deflection or “bow”. This type affects flights pushing sludge or surface scum. If a flight is too bowed in the middle, it can lead to attachment link breakage and permanent flight deformation.
- Vertical deflection or “sag”. Too much sag in the flight board can wear out the middle of the scraper lip and increase system loading. Excessive sag can eventually lead to premature chain wear and may even cause a tank crash.
Two key characteristics in determining a flight’s rigidity are the Modulus of Elasticity (E) and Moment of Inertia (I). The Modulus of Elasticity is a measure of material stiffness. The Moment of Inertia measures an object’s resistance as it rotates on its axis. Deflection is inversely proportional to the Modulus of Elasticity multiplied by the Moment of Inertia, or E x I. A higher EI value translates to less deflection and a stiffer flight. Comparing EI values of various flight profiles can help you select the correct option.
Note that some suppliers only specify the Moment of Inertia of their profile. While the Moment of Inertia of their specified flight may look impressive, they may be offering a substandard material with a less-than-ideal Modulus of Elasticity. You must consider both when deciding on the right flight for your application.
5. Quality Assurance
When choosing a supplier, specify one with a quality assurance procedure that defines the flight’s specifications and other system equipment. Too often, suppliers will cut corners to be cost-competitive in the market, sacrificing quality and longevity. A quality assurance specification is the best way to identify that your flights will perform how you want them to. Brentwood’s flight specification defines machining tolerances and criteria, what possible cosmetic defects are admissible, sets mechanical and physical property requirements, and defines inspection and ASTM testing protocols. Insist that any flight supplier has procedures in place to ensure the quality and standards of your next scraper profile.
Making Your Selection
There are several factors to consider when purchasing and specifying new flights. It’s important to review each of them to ensure that you will be receiving a quality product that performs efficiently. While all considerations mentioned are keys to this, deflection is the single largest concern you should have when evaluating new flight options. Having peace of mind in your selection boils down to obtaining the right process data on your system, providing accurate tank dimensions, and working with Brentwood’s Polychem team to calculate the best profile option for your site-specific needs. We consider all loading situations to ensure that not only are your flights correct, but that your chains, shafts, sprockets, and other system equipment are suitable for the system conditions.
Check out our product page to learn more about the specific Polychem flight profiles Brentwood offers. When you’re ready to upgrade, reach out to us and we’ll help recommend the best flight profile for you.
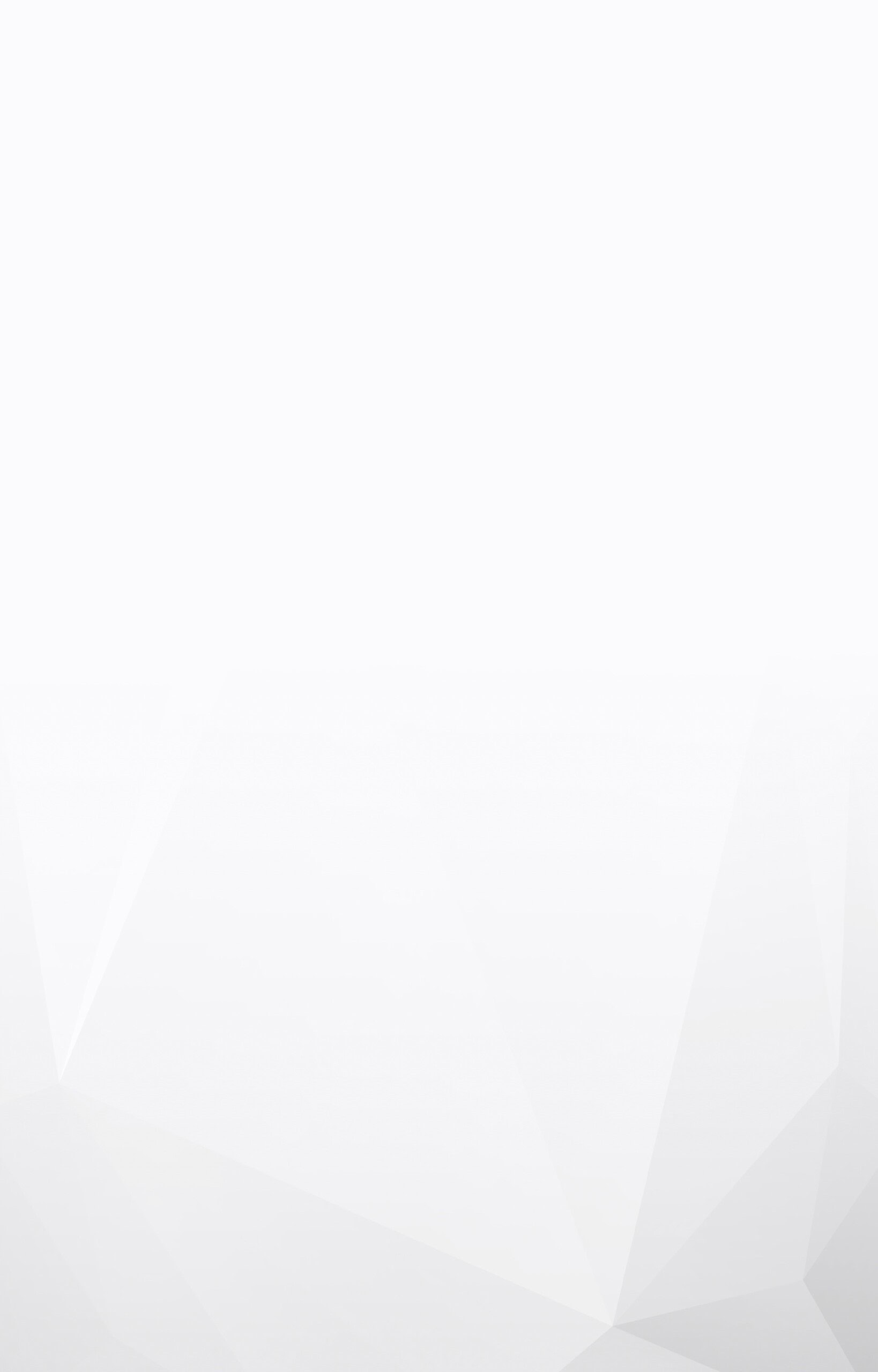